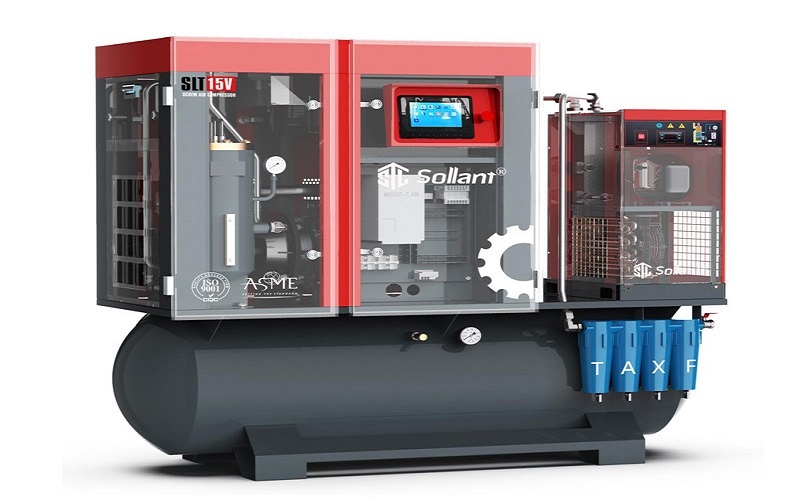
How to Choose Air Compressor for Laser Cutting Machine
Introduction to Laser Cutting Machine
Since the emergence of laser cutting machines, the world’s laser cutter industry has been growing rapidly. More and more sheet metal processing enterprises, kitchen & bathroom manufacturing, automobile parts processing enterprises are using laser cutting machines, especially the sheet metal processing industry. Laser cutting is to replace the traditional mechanical knife with invisible beam, with high precision, fast cutting, not limited to cutting pattern limitation, automatic typesetting saving material, smooth cut, low processing cost, etc. And the air compressor can provide power for the laser cutting machine.
Principle of Laser Cutting Machine
First of all, we introduce the cutting principle of laser cutting: the laser produced by the oscillator passes through the lens and converges at one point to form a very small spot. By accurately controlling the distance between the lens and the plate, the laser spot is stable in a certain position in the direction of material thickness.
The commonly used auxiliary gases are oxygen, nitrogen, and compressed air, argon is sometimes used.
Because of the combustion of oxygen, so cutting thicker carbon plates requires oxygen, the purity requirement is generally 99.5% or higher, but because of oxygen, will produce a clear oxide film at the end of the incision, quenching effect around the cutting surface, have a certain impact on subsequent processing, the end face of the incision is black or dark yellow.
Use nitrogen to cut stainless steel or aluminum plates. The effect is to prevent oxidation and blow off the melt. High purity of nitrogen (especially stainless steel above 8 mm, Requirements to achieve 99.999% purity) pressure requirements are relatively large, general requirement 1 Mpa.
If you want to cut more than 12 mm, or stainless steel as thick as 25 mm, the pressure is higher, 2Mpa above or higher. Will form a protective layer around the metal that cuts the material, the end face of the incision is white.
Argon is the same as nitrogen, as inert gas, It can also prevent oxidation and nitridation in laser cutting. General laser cutting using argon is extremely uneconomical, argon cutting is mainly used in titanium and titanium alloys.
If the auxiliary gas uses compressed air, we know that there is already about 21% oxygen and 78% nitrogen in the air.
In terms of cutting speed, there is no speed of pure oxygen melting cutting, and in terms of cutting quality, there is no pure nitrogen protection of the cutting method effect.
But this can be reversed from a positive point of view: the auxiliary gas uses compressed air to cut faster than nitrogen protection, and the cutting quality is better than oxygen cutting.
Most importantly, compressed air can be supplied directly by a laser air compressor, which is easier to obtain than oxygen, nitrogen, argon.
If you buy an air compressor system —— laser cutter air compressor, the initial investment will be higher. But with a simple accounting, it is easy to conclude that long-term laser cutting machines are used for processing, if not for speed, or for high-quality requirements, auxiliary gases for laser cutting machines.
Using compressed air is very cost-effective, and compressed air can also be used as a cylinder power source and optical path positive pressure dust removal, and there is no risk of gas leakage.
If the auxiliary gas uses compressed air, we know that there is already about 21% oxygen and 78% nitrogen in the air.
In terms of cutting speed, there is no speed of pure oxygen melting cutting, and in terms of cutting quality, there is no pure nitrogen protection of the cutting method effect.
But this can be reversed from a positive point of view: the auxiliary gas uses compressed air to cut faster than nitrogen protection, and the cutting quality is better than oxygen cutting.
Most importantly, compressed air can be supplied directly by air compressor, which is easier to obtain than oxygen, nitrogen, argon.
If you buy an air compressor for laser cutting machine, the initial investment will be higher. But with a simple accounting, it is easy to conclude that long-term laser cutting machines are used for processing, if not for speed, or for high-quality requirements, auxiliary gases for laser cutting machines. Using a laser cutter air compressor is very cost-effective, and compressed air can also be used as a cylinder power source and optical path positive pressure dust removal, and there is no risk of gas leakage.
How to Choose the Air Compressor for Fiber Laser
When it comes to laser cutter air compressors, many laser cutting users may have questions about how to choose the type of air compressor to match the laser cutting machines correctly.
Generally from the exhaust volume, we should choose a larger air compressor than the actual use, but do not blindly pursue the air volume, if the air compressor exhaust volume is too large, much larger than the actual demand, even if the air compressor has frequency conversion regulation, It may cause air compressor to run at the lowest frequency.
In order to maintain the stability of gas supply pressure, once the gas continues, the air compressor has to start operation. Such frequent “start-working-dormancy-start-working-dormancy “, easy to cause bubbles and emulsification of lubricating oil in oil and gas separator, which will shorten the life of air compressor and increase the oil content of exhaust port.
In terms of pressure, when the laser power is large enough, the higher the pressure, the better the cutting quality and the higher the cutting efficiency. But if the laser power is not large enough, no matter how high the pressure will not help, after all, the laser power is large enough to melt the cutting material faster.
Also most importantly, the quality of compressed air has a very direct effect on the quality of laser cutting. The compressed air contains water mist and oil. If it is not treated clean, high pressure spray onto the protective mirror of the laser cutting head.
A superpower laser cutting machine may also burn out the laser head. At present in the industry, laser cutting machines launched special products. Usually, the micro-oil twin-screw and post-processing equipment are combined to form a complete air source system, which we call a four-in-one laser cutting air compressor.
According to some commonly used configuration, we take carbon steel as an example, roughly statistics the standard of selecting a special air compressor for laser cutting machine:
Note:
Specific selection should be based on cutting materials and thickness, for more information, please visit our website:www.shanghaisollant.com