Blog
- Home
- Industrial
- Application of Air Compressor in Iron and Steel Industry
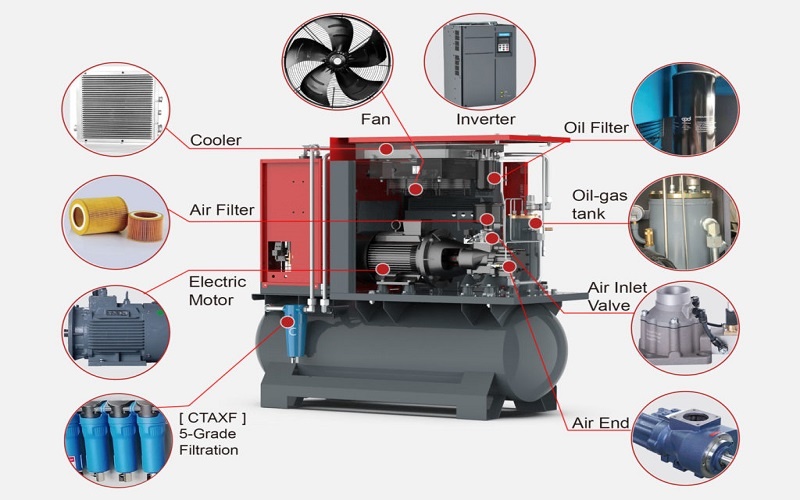
Application of Air Compressor in Iron and Steel Industry
The iron and steel industry refers to the industry that produces pig iron, steel, steel, industrial pure iron and ferroalloys, and is one of the basic industries in all industrialized countries in the world. Economists usually regard steel output or per capita steel output as an important indicator of various countries’ economic strength.
The steel industry is one of the pillar industries of a country. It belongs to heavy industry, and the scale of these enterprises is very large, usually with tens of thousands or hundreds of thousands of people. The construction of a steel company usually takes years or even decades.
The equipment adopted by the new iron and steel enterprises is the most advanced, while the equipment of some old iron and steel enterprises needs to be modified to improve the production efficiency of the enterprises and make the old enterprises glow with new vitality. In this process, the compressor is inseparable everywhere.
A large iron and steel enterprise generally starts from the ore entering the plant to smelting shaped steel ingots and iron ingots, or further processing into steel plates, steel wires, or other shaped steels.
As a typical large-scale industrial enterprise with high energy consumption, iron and steel enterprises account for a large proportion of all energy consumption (approximately 5%-15% of total energy consumption). In steel companies, compressed air is widely used as an energy medium.
The use of compressed air in steel companies is included in all production processes. Its main uses can be divided into sintering pneumatic conveying, blast furnace injection, continuous casting steam spray cooling, bottom blowing of the converter, surface blowing of steel belt, various pneumatic instrument valves, air motors, pulse bag filters, etc.
In the iron and steel production process, the ore is first sintered, and then the sintered iron ore is transported to the kerosene iron blast furnace to be smelted into molten iron and cast into iron ingots.
To make steel ingots, the iron ingots must be sent to the steelmaking blast furnace for re-smelting, changing from iron to steel. If you want to obtain other alloy steels, you must add appropriate elements in the smelting process to make different types of alloy steels.
A large iron and steel enterprise has many sintering workshops (or plants), iron-making blast furnaces, steel-making plants, etc., and they are widely distributed. Therefore, many air compressor stations are set up in general iron and steel enterprises to meet the gas demand of various gas points.
On the one hand, each air compressor station is relatively independent and easy to manage; on the other hand, it can meet the needs of different compressed air quality.
General steel enterprise air compressor station configuration:
The types of air compressors used by iron and steel enterprises generally include centrifugal and screw compressors. At present, piston air compressors have been basically eliminated.
The centrifuge air compressor station is generally equipped with 2-9 centrifuges, usually with a displacement of 100-300m³/min. According to production needs, it is generally set below 1.3Mpa, of which 0.38MPa and 0.5Mpa are used for steelmaking and continuous casting, 0.8 MPa is for power/instrument use, and 1.3Mpa is for coal injection blast furnace.
The screw compressor air compressor station is generally equipped with 2-8 screw compressors, most of which have an air displacement of less than 10-40m³/min. The screw air compressor is mainly used as an auxiliary air source for the centrifugal air compressor.
Uses and characteristics of compressed air in iron and steel enterprises:
The distribution of compressed air in the ironmaking equipment of iron and steel enterprises is mainly in the sintering zone, raw material zone, coke oven zone, and blast furnace zone.
The compressed air in the steelmaking equipment of iron and steel enterprises is mainly used for continuous casting, converter pneumatic and purging, and aerosol cooling for continuous casting.
The hot rolling mill’s compressed air is mainly used for rolling mill and furnace pneumatic equipment and cold rolling purging. Used for strip steel cleaning, pickling, continuous winding, pneumatic equipment and hot-dip galvanizing equipment.
A large amount of compressed air is also required for the injection of coal ash required for ironmaking blast furnace and blast furnace combustion.
For example, a 2500m³ ironmaking blast furnace usually requires 4 40m³/min screw air compressors, of which 3 are normally open and one is used as a standby machine.
The blast furnace’s blowing equipment generally selects a high-pressure fan, usually with a pressure of 0.2 MPa. The amount of compressed air used for conveying coal to the blast furnace.
The quality requirements of compressed air for iron and steel enterprises:
The quality of compressed air demanded by iron and steel enterprises is usually not too high. Except for some of the compressed air used in instruments that require refrigerating dryers, most of them do not need to be processed too precisely.