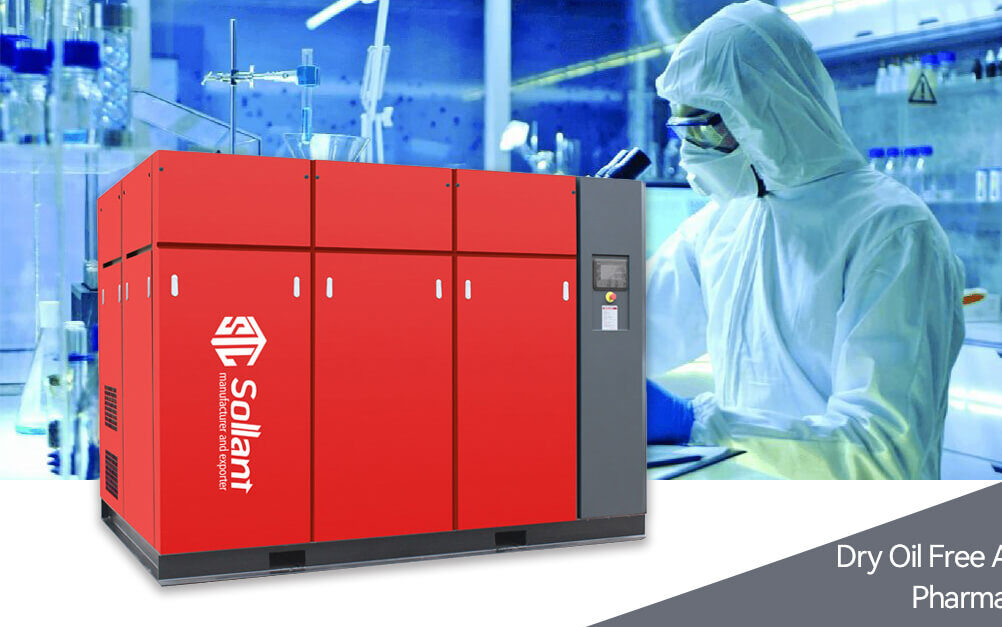
Correct maintenance, maintenance and replacement of air compressor accessories
- Maintenance and maintenance of intake air filter
The air filter is a component that filters out air dust and dirt, and the filtered clean air enters the screw rotor compression chamber for compression. Due to the internal clearance of the screw machine, only particles within 15u are allowed to filter out. If the air filter element is clogged and damaged, a large number of particles larger than 15u will enter the screw machine to circulate, which will not only greatly shorten the service life of the oil filter element and oil-fine separator, but also cause a large amount of particles to directly enter the bearing cavity, which will accelerate bearing wear and increase the rotor clearance. The compression efficiency is reduced, and even the rotor is dry and seized.
It is best to maintain the air filter element once a week. Unscrew the gland nut, take out the air filter element, use 0.2-0.4Mpa compressed air to blow out the dust particles on the outer surface of the air filter element from the inner cavity of the air filter element, and use a clean rag Wipe off the dirt on the inner wall of the empty filter housing. Reinstall the air filter element, and pay attention that the sealing ring at the front end of the air filter element should fit tightly with the inner end surface of the air filter housing. The maintenance of the diesel intake air filter element of the diesel-powered screw machine should be carried out simultaneously with the air compressor air filter element, and the maintenance method is the same.
Under normal circumstances, the air filter element should be replaced every 1000-1500 hours. In places where the environment is extremely harsh, such as mines, ceramic factories, cotton spinning factories, etc., it is recommended to replace the air filter element every 500 hours.
When cleaning or replacing the air filter element, the parts must be combined one by one to prevent foreign matter from falling into the intake valve.
In normal times, it is necessary to check frequently whether the intake expansion tube is damaged or flattened, and whether the connection between the expansion tube and the air filter intake valve is loose or leaking. If found, it must be repaired and replaced in time.
- Replacement of oil filter
After the new machine runs for 500 hours for the first time, the oil element should be replaced, and the oil filter element should be removed by reverse rotation with a special wrench. It is best to add screw oil before installing the new filter element.
It is recommended to replace the new filter element every 1500-2000 hours. It is best to replace the oil filter element at the same time when changing the engine oil. When the environment is harsh, the replacement cycle should be shortened.
It is strictly forbidden to use the oil filter element beyond the time limit, otherwise, due to the serious clogging of the filter element, the pressure difference exceeds the tolerance limit of the bypass valve, the bypass valve will automatically open, and a large amount of stolen goods and particles will directly enter the screw host with the oil, causing serious consequences.
The replacement of the diesel engine oil filter element and the diesel filter element of the diesel-driven screw engine should follow the maintenance requirements of the diesel engine, and the replacement method is similar to that of the screw engine oil element.
- Maintenance and replacement of oil and fine separator
The oil-fine separator is a component that separates the screw lubricating oil from the compressed air. Under normal operation, the service life of the oil-fine separator is about 3000 hours, but the quality of the lubricating oil and the filtration accuracy of the air have a huge impact on its life. It can be seen that the maintenance and replacement cycle of the air filter element must be shortened in harsh operating environments, and even the installation of a front air filter must be considered.
The oil-fine separator must be replaced when it expires or the pressure difference between the front and back exceeds 0.12Mpa. Otherwise, the motor will be overloaded, and the oil and fine separator will be damaged and oil will leak out.
Replacement method:
(1) Remove the control pipe joints installed on the oil and gas barrel cover. Take out the oil return pipe extending into the oil and gas barrel from the cover of the oil and gas barrel, and remove the fastening bolts of the upper cover of the oil and gas barrel.
(2) Remove the upper cover of the oil and gas barrel, and take out the oil and fine separator. Remove the asbestos pad and dirt stuck on the upper cover.
(3) Install a new oil and fine separator, pay attention to the upper and lower asbestos pads must be stapled and stapled, and the asbestos pads must be placed neatly when pressing, otherwise it will cause pad flushing.
(4) Reinstall the upper cover plate, oil return pipe, and control pipes as they were, and check for leakage.
- Maintenance and replacement of screw oil
The quality of the screw oil has a decisive influence on the performance of the oil-injected screw machine. Good oil has good oxidation stability, rapid separation, good foam cleaning, high viscosity, and good anti-corrosion performance. Therefore, users must use pure The company’s special screw oil.
After the running-in period of the new machine is 500 hours, replace the oil for the first time, and then replace with new oil according to the instructions for use. It is best to replace the oil filter at the same time when changing the oil. Use in places with harsh environments to shorten the replacement cycle.
Replacement method:
(1) Start the air compressor and run it for 5 minutes, so that the oil temperature rises above 50°C and the viscosity of the oil decreases.
(2) Stop running, when there is no pressure of 0.1Mpa in the oil and gas barrel, open the oil drain valve at the bottom of the oil and gas barrel, and connect the oil storage tank. The oil drain valve should be opened slowly to avoid splashing of lubricating oil under pressure and hurting people and dirt. Close the oil drain valve after the lubricating oil is in the form of drops. Unscrew the oil filter element, drain the lubricating oil in each pipeline at the same time, and replace it with a new oil filter element.
(3) Open the screw plug of the fuel filler, inject new oil, make the oil level within the range of the oil scale, tighten the screw plug of the fuel filler, and check for leakage.
The lubricating oil must be checked frequently during use. When the oil level line is found to be too low, new oil should be replenished in time. The condensed water must also be discharged frequently during the use of the lubricating oil. Generally, it should be discharged once a week, and it should be 2-3 days in high temperature climates. Discharge once. Shut down for more than 4 hours, open the oil release valve when there is no pressure in the oil and gas barrel, drain the condensed water, and close the valve quickly when you see organic oil flowing out.
It is strictly forbidden to mix different brands of lubricating oil, and do not use the lubricating oil for an extended period of time, otherwise the quality of the lubricating oil will deteriorate, the lubricity will be poor, and the flash point will be lowered, which will easily cause high-temperature shutdown and spontaneous combustion of the oil.
- Maintenance of cooler
The cooling effect of the cooler directly affects the operating temperature of the air compressor. The plate-fin structure is easy to accumulate dust, so the maintenance of the cooler needs to be blown from top to bottom with dry compressed air above 0.4Mpa every shift. The diesel-driven screw cooler is upright. During maintenance, it needs to be blown from the outside to the inside with dry compressed air above 0.4Mpa. After blowing, clean the dust and particles in the air guide cover to prevent it from being blown by the fan again. Blow into the cooler and cause blockage, causing high temperature of the machine. If the machine is used in a harsh environment and the surface of the cooler is full of oil, it must be cleaned with a carbon cleaning agent.
- Minimum pressure valve (pressure maintenance valve) cleaning
Although the minimum pressure valve in the screw air compressor looks relatively small, it controls the whole machine regardless of its small size. In order to allow it to work normally under normal work, the maintenance method of the minimum pressure valve of the screw air compressor is provided below.
The minimum pressure valve is composed of a valve body, a valve core, an adjusting nut, a spring, and a sealing element. The minimum pressure valve is mainly used to establish the internal pressure of the unit, promote the circulation of lubricating oil, and meet the working pressure of the unloading valve. In addition, the minimum pressure valve also acts as a check valve to prevent the compression of the gas storage tank when the unit is unloaded. Air flows back to the air compressor.
The structure of the minimum pressure valve is very simple. Unscrew the nut of the screw air compressor between the valve core and the valve body to take out the components inside. The minimum pressure valve core of the small unit is built into the valve body. All internal components can be taken out.
The minimum pressure valve can be cleaned according to the method of cleaning the unloading valve.
Since the structure of the minimum pressure valve is very simple, the assembly process will not be described one by one, but it should be noted that if there is a U-shaped ring inside, pay attention to the direction of the U-shaped ring. After the cleaning process of the minimum pressure valve of the screw air compressor is completed, put it aside to be installed in the air compressor.
- Oil return check valve cleaning
The check valve is composed of valve body, steel ball, steel ball seat, spring and other components. The oil-gas mixture compressed by the main engine of the air compressor is firstly separated by centrifugal force in the oil-gas tank. Because the weight of the oil is greater than that of air, most of the oil in the solid-oil-gas mixture falls to the oil tank by centrifugal force, and the screw air compressor then Under the action of internal pressure, it returns to the main engine for the next lubrication cycle process, and the compressed air containing a small amount of oil is separated again by the oil-air separator. At this time, the lubricating oil separated by the oil-air separator will fall to the bottom of the oil-air separator. To prevent this part of the oil from being taken away with the compressed air, the unit is designed with an oil pipe inserted into the bottom of the oil-gas separator, through the internal pressure, this part of the oil is directly introduced into the main engine for lubrication, and there is a one-way valve on the oil pipe, the screw The air compressor is called the oil return single-way valve.
Its function is to smoothly recycle the oil from the oil-gas separator to the main engine without letting the oil of the main engine flow back to the oil-gas separator. The oil return single-way valve has a joint on the valve body, unscrew it from the joint, and take out the spring, steel ball and steel ball seat.
Clean the oil return one-way valve: Clean the valve body, spring, steel ball, steel ball seat with cleaning agent, and some check valves have filter screens inside, if any, clean them together.
- Screw air compressor cleaning temperature control valve
The temperature control valve is composed of valve body, valve core, temperature sensing element, spring and so on. The temperature control valve plays the role of constant temperature control. When the oil temperature measured by the temperature sensing element of the temperature control valve is lower than the operating value (the operating value of the temperature sensing element is generally 71 degrees), the lubricating oil returns directly from the oil and gas barrel to the main engine. When the oil temperature measured by the temperature sensing element of the temperature control valve is higher than the operating value, the thimble of the temperature sensing element of the temperature control valve will act, and push the valve core to open the bypass valve equipped with itself, so that the lubricating oil enters the cooler for cooling (if the temperature sensing element detects The higher the temperature, the greater the opening of the bypass valve), and the cooled lubricating oil returns to the main engine.
There is a cover on the front surface of the temperature control valve of the screw air compressor, and there are screw holes on the cover. Find a suitable nut and screw it into the cover. Screw in the nut, you can take off the cover and all the internal parts. Clean all parts of the temperature control valve according to the method of cleaning the unloading valve.
After all the above parts are cleaned and dried, they are installed on the air compressor. After all the parts are installed on the air compressor, check again for any omissions and clean up the tools and other items used during installation.
Sollant Group-Professional Compressed Gas Solutions Provider