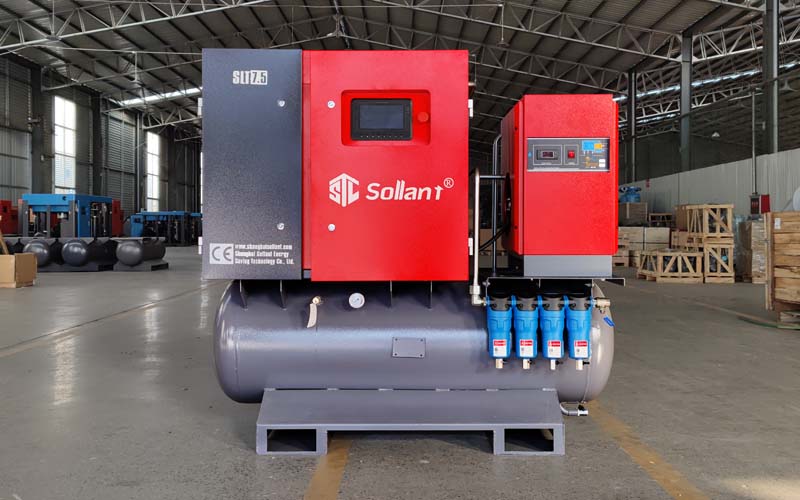
How about the energy saving effect of frequency conversion screw air compressor?
Sollant permanent magnet variable frequency screw air compressors have reached the first-class energy efficiency standard, the whole machine system is optimized, and the energy-saving effect is industry-leading. The average power-saving effect can reach more than 30%-50%.
High-efficiency and energy-saving host: industry-leading high-quality screw host, high efficiency, high reliability, long life, low energy consumption, low noise, and low maintenance cost.
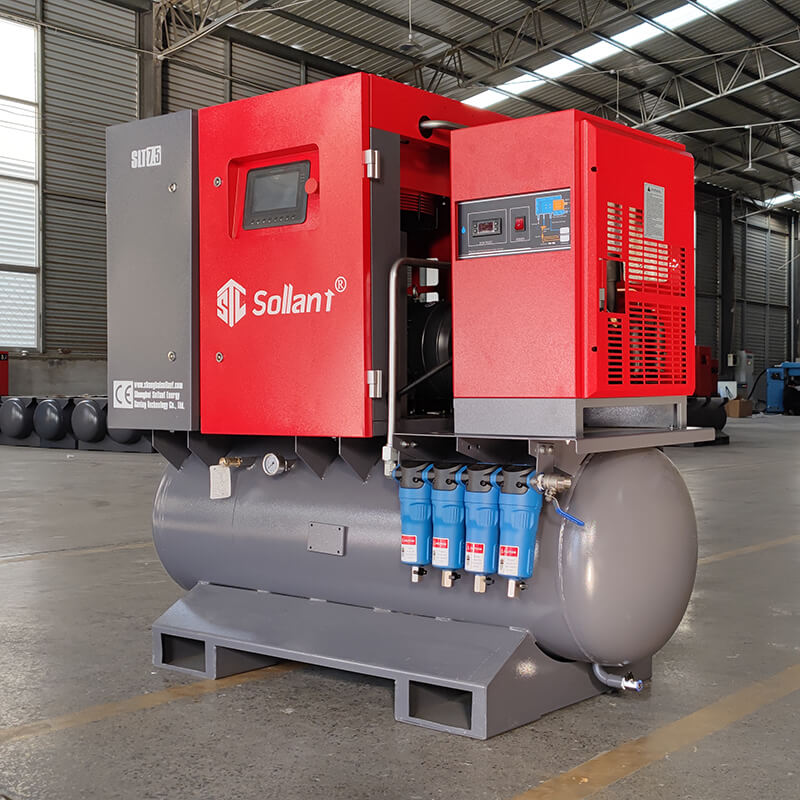
High-efficiency permanent magnet motor: high efficiency, 7-12% higher than ordinary asynchronous motors; high protection, protection class IP54, safer and more durable; high precision, fast response, matching the whole machine system.
High-performance vector inverter: domestic first-line brand heavy-duty inverter, infinitely variable, frequency conversion range from 25%-100%, built-in reactor, to improve the quality of the power grid.
The permanent magnet variable frequency screw air compressor is the hottest air compressor product in the air compressor market, and it is the focus of attention of the majority of merchants and users. Users with increasing awareness of energy conservation tend to purchase and use permanent magnet variable frequency air compressors to replace high-energy-efficiency air compressor products. So what is the energy saving effect of the permanent magnet variable frequency screw air compressor?
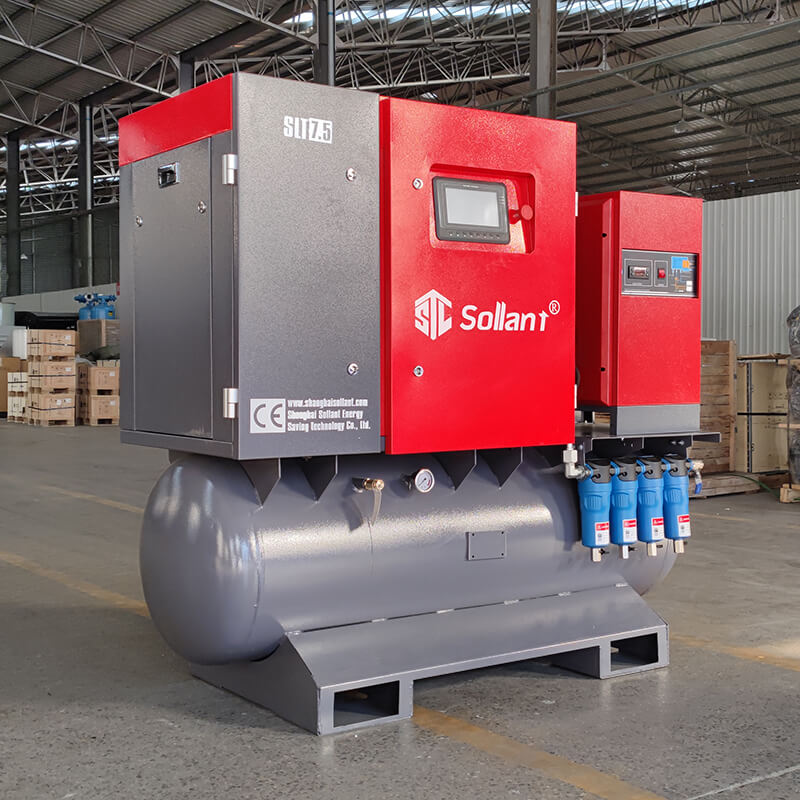
1. The characteristic of permanent magnet variable frequency air compressor is energy saving. Generally, the energy-saving effect reaches 33% and above. It mainly depends on the working conditions and the parameters of the inverter. When the gas pressure of the customer is unstable and fluctuates greatly, the energy-saving effect will be better.
2. Stable air pressure Since the variable frequency screw air compressor utilizes the stepless speed regulation characteristics of the frequency converter, it can be started smoothly through the controller or the PID regulator inside the frequency converter. Adjust the response.
3. The integrated shaft transmission efficiency of the host and the motor is 99.9%, no coupling, no gear, no belt drive. Permanent magnet motors do not require bearings, maintenance, and lubricants, eliminating fault points and reducing maintenance costs. Ordinary asynchronous motors often suffer from bearing wear and lead to coil burning and other faults, and the maintenance cost is high.
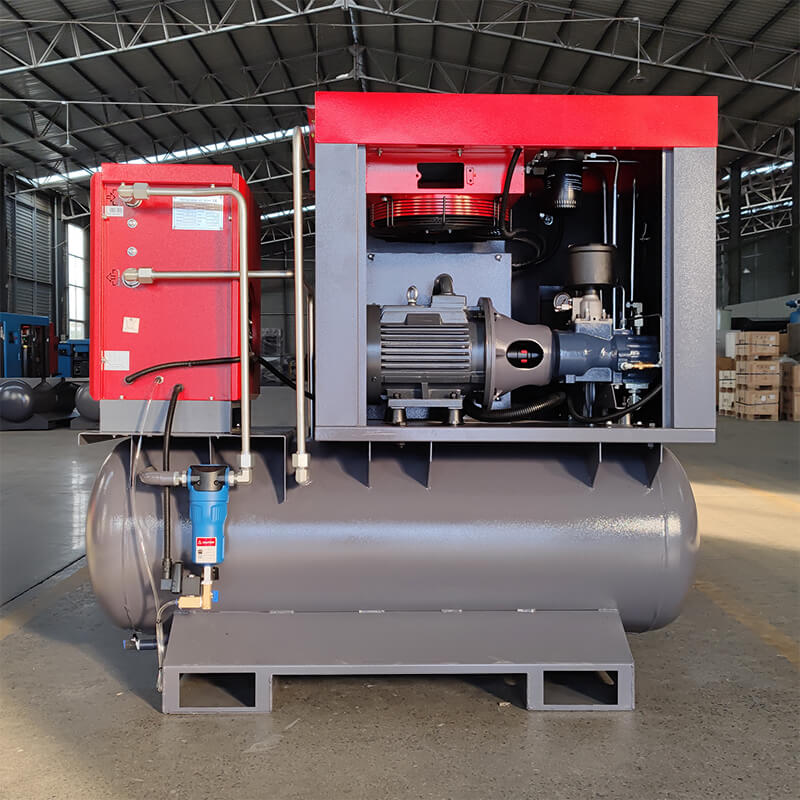
4. No impact current at start-up The frequency converter itself covers the function of soft start, the start-up current is within 2 times of the rated current, and the start-up impact is very small. The power frequency start is generally more than 6 times the rated current. When the capacity of the factory power grid is limited, it will cause the air compressor switch to trip. Not only the impact on the grid, but also the impact on the entire mechanical system is greatly reduced.
5. Variable flow control Ordinary industrial frequency air compressors can only work at one displacement, while permanent magnet variable frequency air compressors can work in a wider range of displacement. According to the actual air consumption, the motor speed is automatically adjusted in real time to control the exhaust volume. How much gas is used to produce as much gas, and the air compressor can be automatically dormant when the gas consumption is low, greatly reducing energy loss.
Sollant Focus on Energy Saving