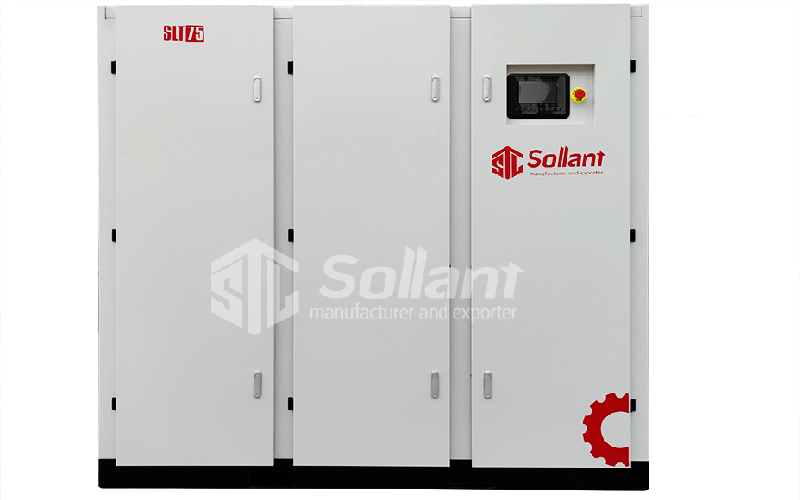
Six unit systems of Sollant screw air compressor
1 .Power system of Sollant screw air compressor
The power system of the air compressor refers to the prime mover and transmission device.
The prime movers of air compressors are mainly electric motors and diesel engines.
Usually the prime mover of the stationary air compressor is an electric motor, while the mobile type has both an electric motor and a diesel engine.
No matter in terms of purchase cost, cost-effectiveness ratio or maintenance operation, electric motors have absolute advantages, so diesel engines are used only in some field constructions, mines, etc. when there is a lack of power supply, and generally only used in pneumatic tools and equipment. on the drive.
There are many transmission modes of screw air compressors, such as belt drive, gear drive, direct drive, integrated shaft drive and so on.
Belt drive (belt)
Belt drive (belt) is usually used on small models, and it was mostly used below 90kW in the early days, but now it is generally used only below 45kW. It is characterized by simplicity, economy, and convenient modification. It does not have high requirements for the manufacturer’s overall machine design and integration capabilities. The disadvantages are that it is noisy, the belt is easy to wear and slip, and the transmission efficiency is lower than other methods.
Gear transmission
Gear transmission is generally used in high-power air compressors (above 110kW) that need to increase or decrease speed. Like belt transmission, it is aimed at occasions that require a speed ratio (transmission ratio). That is, the speed of the motor is different from the speed of the machine head (male rotor). Usually the gear and the host are arranged in a casing.
Direct transmission
Direct transmission, that is, the shaft of the motor and the main engine is transmitted through a coupling. The couplings used in the industry are all flexible couplings, which allow a certain deviation in the alignment of the two rotors. And there are various types, such as plum blossom type, tire type coupling and so on.
The so-called “1:1 direct connection” is a commercial slogan in the industry, which means that the transmission ratio is 1. That is to say, the shaft of the motor is connected to the shaft of the male rotor of the main engine through the coupling. That is, the speed of the host is equal to the speed of the motor, which is used to indicate that the speed of the host is low, and the specification of the host is large. It is not a short-lived machine with a small head and high speed, and it is worth the money.
However, if two transmission modes of gear and direct coupling are actually adopted. Since the host and the gear are integrated, it seems that the motor and the host are directly connected. As shown in the figure below, it cannot be said that it is a 1:1 direct connection.
Integrated shaft transmission
Integrated shaft transmission is a transmission mode that has appeared with the permanent magnet integrated machine in recent years, that is, the shaft of the motor and the shaft of the main machine are the same shaft, and the extending shaft of the main machine is the rotor of the motor, which is completely direct transmission.Compared with the direct drive, it is much shorter in size, which facilitates the miniaturization layout of the whole machine. (missing center bracket and coupling locations).
2 .Host of Sollant screw air compressor
The host of the oil-injected screw air compressor is the core of the whole unit, including the compressor host and its related accessories, such as oil cut-off valves, check valves, etc.
At present, the screw hosts on the market are divided into two types:
single-stage compression and double-stage compression in terms of working principle. As for various integrated innovative models, such as all-in-one machines, the working principle has not changed in essence. The most significant difference in structure between single-stage compression and double-stage compression is: single-stage compression has only one pair of male and female rotors, while two-stage compression has two pairs of male and female rotors.
Single stage compression:
The single-stage compression screw host completes the gas compression process through a single compression chamber.
After the air enters the screw host, it is gradually compressed by the action of a single screw rotation, so that the volume decreases and the pressure increases at the same time.
The final compressed gas is discharged directly from the single-stage compression chamber.
Two-stage compression:
The screw host with two-stage compression uses two compression levels, that is, two compression chambers to complete the gas compression process.
The air first enters the first-stage compression chamber, and under the action of the first-stage screw, the air is initially compressed and the pressure increases, but the required final pressure is not reached. Then, the pre-compressed gas enters the second-stage compression chamber, and under the action of the second-stage screw, the gas is compressed again to the required final pressure. The final compressed gas is discharged from the second stage compression chamber.
Two-stage compression has some advantages over single-stage compression. Since the gas is compressed separately in two stages, the compression ratio of each stage is relatively small, which reduces the power consumption of each stage. This increases the efficiency of the entire screw airend and is suitable for applications requiring higher pressures. In certain industrial processes with high pressure gas supply requirements, a two-stage compression screw air end is usually the more common choice.
At present, the two-stage compression hosts on the market mainly have two structures: upper and lower, and front and rear, among which the upper and lower structures are the most common. The so-called “split” structure of two permanent magnet motors with two hosts still needs to be further tested by the market.
3. Intake system of Sollant screw air compressor
The air compressor intake system mainly refers to the compressor sucking in the atmosphere and its related control components.
It usually consists of two parts: the intake filter unit and the intake valve group.
1.The intake filter unit is relatively simple in structure, usually consisting of an air filter and an intake duct (both soft and hard). Some small machines do not have an air intake duct, and do not even need an air filter housing, but directly install the air filter element on the intake valve. Units with larger flows will also use multiple sets of air filters to obtain better filtering effects and reduce suction resistance.
The function of the air filter is literally, to filter the air inhaled by the compressor. This filter mainly refers to the filtration of solid particles such as dust and debris in the inhaled air.
The filter element of the air filter is a consumable item. The maintenance of the screw air compressor is “three filters and one oil”, that is, “air filter element, oil filter, oil fine separator element and air compressor oil”.
2.The intake valve group is installed on the intake port of the compressor main unit, and is used to control the amount of inhaled air to achieve different working states such as loading, unloading, and proportional adjustment of the air compressor.
The intake valve group usually consists of a valve body, actuators such as cylinders and control components such as solenoid valves.
There are various forms of intake valves, and the commonly used ones are piston type and butterfly type according to the valve body structure.
- The piston-type intake valve uses the up and down or left and right movements of the piston in the intake valve to control the intake of the air compressor. Usually, it only has two states of open/close, and is generally used in small flow situations.
- The main structure of the butterfly intake valve is a butterfly valve, and the moving part is a valve plate, which is pushed by the push rod of the servo cylinder, and the inlet flow can be controlled by controlling the opening/closing and opening of the valve plate. Usually used in larger flow occasions.
4. Cooling system of Sollant screw air compressor
Air compressor cooling methods are air-cooled and water-cooled. There is no good or bad between air-cooled and water-cooled, only applicable and not applicable.
- Water cooling requires the owner to have a cooling water system, while air cooling is more flexible in layout, but there is also a requirement for good ventilation in the installation site;
- The cooling effect of the water-cooled model depends entirely on the cooling water system. If the cooling water system of the owner company is in normal operation, the cooling effect is very stable and reliable. Air cooling is greatly affected by the ambient temperature and the installation environment, but usually the extreme conditions have been considered in the design of the manufacturer, so the installation according to the requirements can also achieve a satisfactory cooling effect.
- The cooling process of the water-cooled air compressor does not require electrical equipment, and does not occupy the energy consumption of the air compressor itself (the circulating cooling water of the owner’s enterprise requires electricity). The air-cooled air compressor needs to be equipped with a cooling fan, which occupies the energy consumption of the air compressor itself.
- Water cooling has high heat exchange efficiency, small size, and is more concise and compact than air cooling. In addition, because air cooling has a cooling fan, the wind noise is larger during work, so water cooling is lower than air cooling.
The medium that the air compressor needs to be cooled is compressed air, and the second is cooling oil (or air compressor oil, lubricating oil, and coolant all mean the same thing), of which the latter is the most critical, it is whether the entire unit can continue to operate stably the key to.
The air compressor oil needs to circulate indefinitely in the body to act as a heat carrier, bringing the heat released by the compressed air during the compression process of the main engine and other heat to the cooler and taken away by the cold medium (wind or water) .
In engineering, almost all air-cooled air compressors use plate-fin coolers. Usually, air cooling and oil cooling are integrated, part of which cools the compressed air (air cooling) and part of the air compressor oil (oil cooling). The water-cooled ones almost all use the shell-and-tube type (or shell-and-tube type), which are divided into oil-cooled coolers and air-cooled coolers.
The air-cooled plate-fin cooler is made of brazed aluminum or aluminum alloy. High-temperature oil and compressed air flow in the cooler, and the heat is taken away by forced convection through the cooling fan.
Water-cooled shell-and-tube (tube-and-tube) cooler, the heat medium is high-temperature oil and compressed air, and the cold medium is cooling circulating water. Through heat exchange, the heat is taken away by the cooling water.
5. Oil and gas separation system of Sollant screw air compressor
In the air compression process of the oil-injected screw air compressor, “oil injection” participates in the compression, there must be a system to separate the oil and the air, keep the oil in the body and continue to circulate, and discharge pure compressed air. The role of the oil and gas separation system is here.
It is precisely because the separation efficiency of the oil-gas separation system reaches an acceptable level that the type of oil-injected screw can be widely used.
The oil and gas separation system of the air compressor is mainly composed of an oil storage tank and an oil and gas separator.
- Working process: The oil-air mixture from the exhaust port of the main engine enters the space of the oil separation tank, and most of the oil gathers in the lower part of the tank through air collision and gravity, and then enters the oil cooler for cooling. The compressed air containing a small amount of lubricating oil passes through the oil-fine separator core to fully recover the lubricating oil, and flows into the low-pressure part of the main engine through the throttling check valve.
6 .Control system of Sollant screw air compressor
The control system of the air compressor includes logic controllers, various sensors, electronic control parts and other control components. To put it vividly, the air compressor control system is the brain, cerebellum, neural network, muscles and tendons, etc. An air compressor without a control system is just a bunch of parts.
At present, there are generally two types of controllers for screw machines (there are almost no pure instruments): one is a single-chip microcomputer, and the other is a PLC.
- The former is generally produced by a special air compressor controller factory to meet the general needs of air compressor control, and the logic program cannot be changed.
- PLC (Programmable Logic Controller) is a general-purpose industrial controller, which needs to realize the air compressor control function through self-programming, and can also meet the unique control requirements of its own products (for air compressor complete machine factories). Sensors used in air compressors are mainly pressure and temperature sensors, and of course differential pressure switches are used in some parts.
The electronic control of the motor is the main part of the control of the air compressor. Simply put, it is to realize the control of the air compressor unit through the power on/off operation of the motor. Including various AC contactors, circuit breakers, transformers, relays, etc., the electronic control part of the main motor is generally called “startup disk”.
The frequency conversion technology is more and more widely used in the industry. This is not only the start and stop control of the motor, but also another control purpose: the control of the motor speed. This part is completed by a frequency converter or an embedded frequency conversion component. Usually, the start/stop of the electric control part of the air compressor that uses frequency conversion is also controlled by the frequency converter, unless it is an air compressor with a dual system of industrial/frequency conversion.
In addition to electrical controls, there are many mechanical controls on the air compressor, such as temperature control valves, minimum pressure valves, etc.