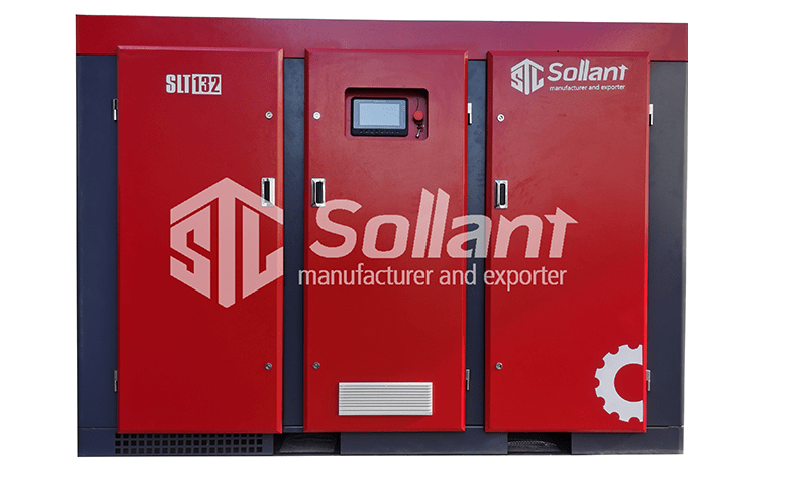
Screw air compressor gas leakage treatment method —Shared by Sollant
Manufacturers who use air compressors will encounter the problem of air compressor oil leakage. There are many reasons for air compressor oil leakage, which causes headaches for users.
Let us share with us various reasons and solutions for air compressor oil leakage :
Minimum pressure failure
If there is a leakage point at the seal of the minimum pressure valve of the air compressor or the minimum pressure valve is opened in advance (because the opening pressure of each manufacturer is different, the general range is between 3.5-5.5kg2), then the machine will build an oil and gas tank at the beginning of operation The pressure time will increase. At this moment, the gas in the low-pressure state has high oil content, and the flow velocity is fast when passing through the oil component. The load of the oil component is increased, and the separation effect is reduced, resulting in high fuel consumption. Screw air compressor Solution: Overhaul the minimum pressure valve and replace if necessary.
The oil separator core is damaged
After the oil separator core is damaged, the oil filtering effect will be reduced, resulting in a large amount of oil leakage. Solution: Replace the oil separator core.
Large gas consumption
Overload and low-pressure use (or the oil treatment capacity selected before the machine leaves the factory is too tightly matched with the machine’s exhaust volume) load and low pressure use means that when the user uses the air compressor, the exhaust pressure does not reach the extra working pressure of the air compressor itself. However, it can basically meet the courage requirements of some enterprise users.
For example, the enterprise users have increased the gas consumption equipment, and the gas consumption has increased, so that the air displacement and the user’s gas consumption cannot reach a balance. Assuming that the air compressor has an additional displacement pressure 8kg, but the pressure in actual use is only 5kg or even lower, so the air compressor is under load for a long time and cannot reach the extra pressure value of the machine, resulting in increased fuel consumption.
The reason is that under the condition of constant displacement , When the oil-air mixture passes through the oil, the flow velocity is too fast, and the oil content in the compressed air is too high, which increases the oil load, resulting in high fuel consumption. Solution: It is recommended to contact the manufacturer to replace an oil product that can match the low pressure application.
The oil level is too high
Too much lubricating oil injected. The amount of oil in the oil-air separator is too high, the distance between the oil separator core and the oil surface is too small, small oil droplets will enter the oil separator core with the compressed air, and the oil-air separation effect will be greatly reduced. Solution: drain the oil to the normal position after removing the pressure.
Improper oil return pipe installation
When replacing, cleaning, and repairing the air compressor, the oil return pipe is not inserted into the bottom of the oil separator (reference: 1~2mm from the bottom of the oil separator is better), so that the separated oil cannot return to the machine head in time, and the accumulated oil will be compressed with The air runs out together. Solution: stop the machine, and after the pressure release returns to zero, adjust the oil return pipe to a reasonable height (the oil return pipe is 1~2mm away from the bottom of the oil separator, and the oil return pipe with an oblique opening can be inserted into the bottom of the oil separator)
The oil return line of the air compressor is blocked
When the oil return line (including the oil return filter of the one-way valve machine on the oil return line) is blocked by foreign matter, the oil condensed at the bottom of the oil component after separation cannot return to the machine head, and the condensed oil droplets are blown up by the air flow , was taken away with the air after parting. These foreign objects are generally caused by solid impurities that fall during installation. Solution: stop the machine, release the pressure of the oil drum to zero, and then remove the fittings of the oil return pipe, and blow away the blocked odor. When installing the oil separator, pay attention to clean the oil and gas barrel cover, and at the same time, pay attention to whether there are solid particles remaining in the four parts of the oil separator core.
The brand “Sollant” specializes in the R&D, manufacturing, sales and after-sales of compressors, oil-free compressors and hosts, special gas compressors, various air compressors and post-processing equipment. Provide customers with high-quality, environmentally friendly and efficient air system solutions and fast and stable technical services. Sollant Corporation is customer-centric. Customer satisfaction is the purpose of our Sollant people.