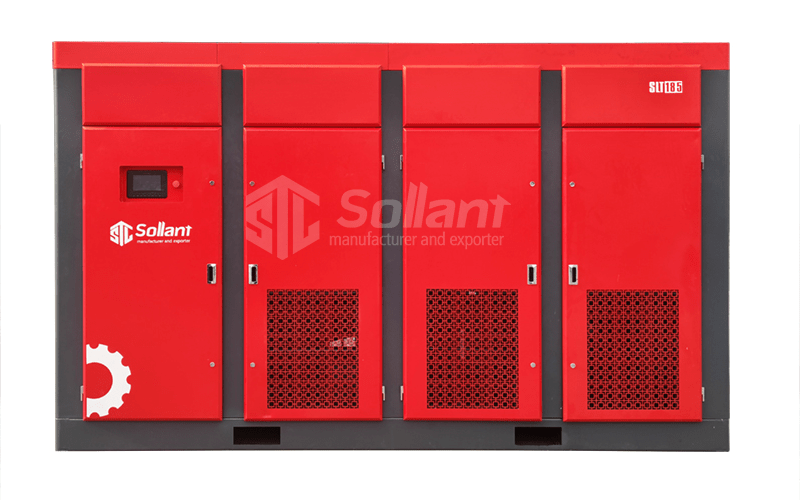
Is the screw air compressor still jumping frequently? —Shared by Sollant
Reasons for frequent jumping of screw air compressors
Air compressor unloading valve failure
The unloading valve is an important part of the screw compressor, and its main function is to control the loading and unloading of the unit, that is, to control the intake air volume of the compressor. The intuitive way to judge whether the unloading valve is closed or not is to remove the air filter, and you can clearly see whether the intake baffle of the unloading valve is closed or open. Most unloading valve failures are that the intake baffle is stuck on the guide rod. At this time, the position of the piston should make the intake baffle close, but the unloading valve cannot be closed because the intake baffle is stuck.
In addition, there are also cases where the intake baffle of the unloading valve is stuck by foreign objects such as mechanical impurities, causing the unloading valve to not close. After removing the air filter, if the air intake baffle is stuck due to mechanical impurities, etc., the unit can be started smoothly after cleaning; if the air intake baffle is stuck on the guide rod, grind the guide rod with sandpaper, and clean it on the guide rod. Apply a small amount of grease on it; if the unloading valve is seriously damaged, you need to replace the unloading valve.
Lubricating oil causes high temperature trip
There is a temperature-sensing probe on the sliding spool of the temperature-controlled bypass valve, which controls the on-off of the spool, and judges that the opening temperature of the temperature-controlled bypass valve is within 70±10°C; The temperature point operates, so that the hot lubricating oil coming out of the air compressor body cannot or all be cooled by the oil cooler and directly returns to the air compressor body, so that the temperature of the air compressor cannot be controlled. When the lubricating oil with impurities passes through the temperature control valve, the sliding core is stuck, so that the valve core cannot be closed, and some oil is directly bypassed to the machine, and the cooling effect is not good.
Start under pressure
Check the mechanical pressure gauge on the oil and gas barrel of the compressor on site. If the pressure gauge shows pressure, it is preliminarily determined that the system may not be depressurized, causing the compressor to start with pressure, resulting in an excessively high starting current, which causes the air switch to trip to protect the unit. Because in the screw air compressor, it often occurs that the pressure in the system still exists after the compressor is shut down due to the failure of the minimum pressure valve or the blockage of the pressure relief system.
There are generally two possibilities for the pressure gauge to show pressure: one is that there is indeed pressure in the system; the other is that the pressure gauge is damaged and cannot be returned to zero normally. The way to judge is to open the device or valve that can relieve pressure in the system. When the pressure relief valve is opened and the pressure gauge in the oil and gas barrel shows that there is still pressure, it is judged that the system has no pressure, and the pressure gauge cannot be reset to zero; otherwise , then the system is under pressure.
Excessive head resistance
Excessive head resistance will cause the compressor to start the current too high, that is, the compressor is overloaded, causing the air switch to trip. The role of lubricating oil in the screw compressor is very important. Its role is mainly manifested in four aspects: cooling, lubrication, sealing, and noise reduction. The quality of the oil and the amount of oil directly affect the normal operation of the compressor. The operation and service life of the compressor, especially the head part of the compressor, are significantly affected.
Electrical device failure
Many users use 380V low-voltage motors, which are started in star-delta switching step-down starting mode. In the early stage, they operate in star mode, and when the compressor starts running for 10 seconds, it turns into delta mode. If the star-delta switch fails, normal star-delta conversion cannot be performed, which will cause the compressor to trip after starting for 10 seconds. In addition, the shortening of the set start time of the air switch due to vibration and other reasons during use may also cause the instant trip of the start.
The brand “Sollant” specializes in the R&D, manufacturing, sales and after-sales of compressors, oil-free compressors and hosts, special gas compressors, various air compressors and post-processing equipment. Provide customers with high-quality, environmentally friendly and Efficient air system solutions and fast and stable technical services. Sollant Corporation is customer-centric. Customer satisfaction is the purpose of our Sollant people.
Sollant Focus on Energy Saving.