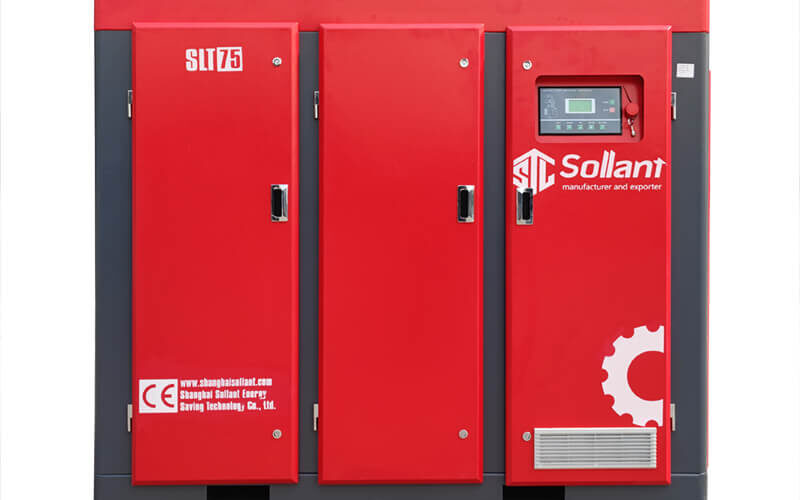
Screw air compressor equipment management assessment index
1. The intact rate of the equipment.
The intact rate of equipment is the most used indicator, but its role in promoting management is limited. The so-called intact rate refers to the ratio of intact equipment to the total number of equipment during the inspection period (equipment intact rate=number of intact equipment/total number of equipment). The indicators of many factories can reach more than 95%. The reason is very simple. At the moment of inspection, if the equipment is in operation and there is no failure, it is considered to be in good condition, so this indicator is very good. Looking good means that there is not much room for improvement, it means that there is nothing to improve, and it means that it is difficult to improve. For this reason, many companies propose to modify the definition of this indicator, for example, propose to check three times on the 8th, 18th, and 28th of each month, and take the average of the intact rate as the indicator of the intact rate for this month. This is certainly better than checking once, but it’s still a good rate reflected in dots. Later, it was proposed that the hours of the intact table be compared with the hours of the calendar table, and the hours of the intact table are equal to the hours of the calendar table minus the total table hours of faults and repairs. This indicator is much more realistic. Of course, there is an increase in the statistical workload and the authenticity of the statistics, and the debate on whether to deduct when encountering preventive maintenance stations. Whether the indicator of intact rate can effectively reflect the status of equipment management depends on how it is applied.
2. The failure rate of the equipment.
This indicator is easy to confuse, and there are two definitions: (1) if it is the failure frequency, it is the ratio of the number of failures to the actual start-up of the equipment (failure frequency = number of failure shutdowns / actual number of equipment startups); (2) if it is failure shutdown The rate is the ratio of the downtime of the fault to the time when the equipment is actually started plus the time of the downtime (the downtime rate = the time of the downtime/(the time when the equipment is actually started + the time of the downtime)). Obviously, the outage rate It can truly reflect the status of the equipment.
3. Equipment availability.
This is widely used in western countries, but in our country there are planned time utilization rate (planned time utilization rate = actual working time/planned working time) and calendar time utilization rate (calendar time utilization rate = actual working time/calendar time) two Different terms. Availability as defined in the West is actually calendar time utilization by definition. The calendar time utilization reflects the full utilization of the equipment, that is to say, even if the equipment is operated in a single shift, we calculate the calendar time according to 24 hours. Because no matter whether the factory uses this equipment or not, it will consume the assets of the enterprise in the form of depreciation. The planned time utilization reflects the planned utilization of the equipment. If it is operated in a single shift, the planned time is 8 hours.
4. The mean interval between failures (MTBF) of the equipment.
Another formulation of this is called the average trouble-free working time (average interval between failures of equipment = total time of trouble-free operation in the statistical base period/number of failures). Complementary to the downtime rate, it reflects the frequency of failures, that is, the health of the equipment. One of the two indicators is enough, and there is no need to use related indicators to measure a content. Another indicator that reflects maintenance efficiency is mean time to repair (MTTR) (average time to repair = total time spent on maintenance in the statistical base period/number of maintenance), which measures the improvement of maintenance work efficiency. With the advancement of equipment technology, its complexity, maintenance difficulty, fault location, average technical quality of maintenance technicians and equipment age, it is difficult to have a definite value for maintenance time, but we can measure its average status and progress based on this .
5. Overall Equipment Effectiveness (OEE).
With the increasingly fierce market competition, manufacturers want to continuously obtain high economic benefits, maximize excavation and improvement. The production efficiency of the production workshop is extremely important, and in some respects, it even becomes the decisive factor for whether the enterprise can make a profit. However, in the current manufacturing industry, the production workshop that seems to be working well is not actually working in the best state, and there is a lot of room for improvement in the value of equipment and operators, which has brought huge benefits to the enterprise virtually. Loss. In order to solve this problem, the international manufacturing industry put forward the concept of overall equipment effectiveness (OEE).
The overall equipment efficiency is Overall Equipment Effectiveness, referred to as OEE. Generally, each production equipment has its own theoretical production capacity, and to realize this theoretical production capacity, it must be guaranteed without any interference and quality loss. It is a strict measure of the overall performance of the machine, indicating where the time waste exists, and the purpose of counting various time wastes is to achieve improvement.
An indicator that reflects equipment efficiency more comprehensively, OEE is the product of the time operating rate, performance operating rate and qualified product rate. Just like a person, the time activation rate represents the attendance rate, the performance activation rate represents whether to work hard after going to work, and to exert due efficiency, and the qualified product rate represents the effectiveness of the work, whether frequent mistakes are made, and whether the task can be completed with quality and quantity . The simple OEE formula is: overall equipment efficiency OEE=qualified product output/theoretical output of planned working hours.
6. Total Effective Productivity TEEP.
The formula that best reflects equipment efficiency is not OEE. Total Effective Productivity TEEP=qualified product output/theoretical output of calendar time, this indicator reflects the system management defects of equipment, including upstream and downstream impacts, market and order impacts, unbalanced equipment capacity, unreasonable planning and scheduling, etc. come out. This indicator is generally very low, not good-looking, but very real.
7. Regarding maintenance and management.
There are relevant indicators to reflect, such as the one-time qualified rate of overhaul quality, repair rate and maintenance cost rate, etc.
(1) The one-time pass rate of the overhaul quality is measured by the ratio of the number of times the overhauled equipment meets the product qualification standard for one trial operation to the number of overhauls. Whether the factory adopts this indicator as the performance indicator of the maintenance team can be studied and deliberated.
(2) The repair rate is the ratio of the total number of repairs after equipment repairs to the total number of repairs. This is a true reflection of the quality of maintenance.
(3) There are many definitions and algorithms of maintenance cost ratio, one is the ratio of annual maintenance cost to annual output value, the other is the ratio of annual maintenance cost to the total original value of assets in the year, and the other is the ratio of annual maintenance cost to current year assets The ratio of the total replacement cost, another is the ratio of the annual maintenance cost to the total net asset value of the year, and the last is the ratio of the annual maintenance cost to the total production cost of the year. I think the last algorithm is more reliable. Even so, the magnitude of the maintenance cost rate cannot explain the problem. Because equipment maintenance is an input, which creates value and output. Insufficient investment and prominent production loss will affect output; of course, too much investment is not ideal, which is called overmaintenance, which is a waste. Appropriate input is ideal. Therefore, the factory should explore and study the optimal investment ratio. High production costs mean more orders and more tasks, and the load on the equipment increases, and the demand for maintenance also increases. Investing in an appropriate ratio is the goal that the factory should strive to pursue. If you have this baseline, the farther you deviate from this metric, the less ideal it is.
8. About spare parts management.
There are many indicators, and the turnover rate of spare parts inventory (the turnover rate of spare parts inventory = monthly consumption of spare parts cost / monthly average spare parts inventory fund) is a more representative indicator. It reflects the mobility of spare parts. If a large amount of inventory funds are backlogged, it will be reflected in the turnover rate. What also reflects spare parts management is the ratio of spare parts funds, that is, the ratio of all spare parts funds to the total original value of the enterprise’s equipment. The value of this value varies depending on whether the factory is in a central city, whether the equipment is imported, and the impact of equipment downtime. If the loss of equipment downtime is as high as tens of millions of yuan a day, or the failure has serious environmental pollution and personal safety hazards, and the supply cycle of spare parts is long, the inventory of spare parts will be higher. Otherwise, the funding rate of spare parts should be as high as possible. reduce. There is an indicator that is not noticed by people, but it is very important in contemporary maintenance management, that is, maintenance training time intensity (maintenance training time intensity = maintenance training hours/maintenance working hours). Training includes professional knowledge of equipment structure, maintenance technology, professionalism and maintenance management etc. This indicator reflects the importance and investment intensity of enterprises in improving the quality of maintenance personnel, and also indirectly reflects the level of maintenance technical capabilities.
Sollant Group-Professional Compressed Gas Solutions Provider