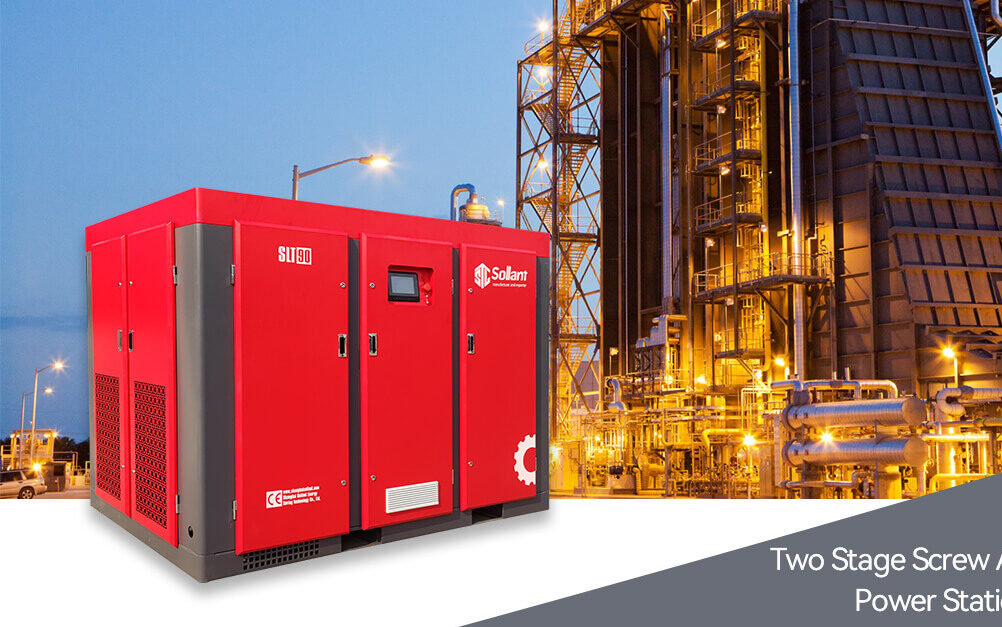
Entering the small heat, the more headache than people getting angry is the high temperature of the air compressor
Envirnmental factor
The impact of high ambient temperature on the temperature of the screw air compressor is mainly manifested in two aspects:
- The higher the temperature, the thinner the air, the lower the working efficiency of the air compressor, and the more time the air compressor is in the loading state, resulting in more heat generated by the air compressor, resulting in high temperature.
- Generally, when the air compressor is designed, there is a design operating environment temperature (30-40°C). When the air compressor is operated at the design operating environment temperature, the highest temperature is usually close to the air compressor protection temperature. If the air compressor environment If the temperature is higher than the design operating environment temperature, the temperature of the air compressor will be increased so that the air compressor will even exceed the shutdown temperature of the air compressor, resulting in high temperature of the air compressor.
Mechanical failure
- The oil stop valve is faulty.
The oil stop valve (also known as the oil cut-off valve) is not working properly, causing the main engine to heat up rapidly due to lack of oil, and in severe cases, the screw assembly will be burned.
- The compressor oil filter is faulty.
First, it affects the supply of compressor oil, resulting in the failure of equipment lubrication and causing high temperature; second, it hinders the normal circulation of compressor oil, affects the heat dissipation of the compressor, and causes high temperature.
- The thermal control valve (temperature control valve) is malfunctioning.
The thermal control valve is installed in front of the oil cooler, and its function is to maintain the exhaust temperature of the machine head above the pressure dew point. If the thermal control valve fails, the lubricating oil may directly enter the machine head without going through the cooler, so that the oil temperature cannot be lowered, resulting in overheating.
- The oil volume regulator of the compressor is abnormal.
The role of the oil volume regulator is to control the oil injection volume of the compressor. If the oil injection volume is too small, the compressor will be overheated. At this time, the oil injection volume should be increased appropriately. However, it should be noted that the oil volume regulator has been calibrated when the equipment leaves the factory, so it is not recommended to use the company’s private adjustment, and it should be adjusted with the equipment manufacturer or by professional maintenance personnel.
- The compressor oil cooler is abnormal.
This fault is common in water-cooled air compressors. Check the temperature difference between the inlet and outlet of the cooler. If the temperature difference is less than 5°C, the heat exchange effect of the cooler will be greatly reduced. The cause of this failure is mostly the blockage or fouling of the cooler. In this case, just remove the cooler for cleaning. For air-cooled air compressors, more attention should be paid to whether the ambient temperature is too high and whether the cooling fan is working abnormally.
- The head of the air compressor is faulty.
Abnormal wear of the air compressor head causes increased heat production and high temperature. There are two common reasons for this failure: one is poor lubrication of the air compressor oil, and the other is the cause of the machine head itself. The solution is to replace the quality air compressor oil, or replace the air compressor head.
- The air filter is faulty.
The air filter is clogged, and the gas production is too small, causing the load of the air compressor to increase, making the air compressor in a loaded state for a long time, increasing heat production, and causing high temperature. At this point the air filter needs to be replaced.
- The oil and gas separator is faulty.
The blockage of the oil and gas separator causes the internal pressure of the air compressor to be too high, resulting in high temperature. There are two reasons for this failure: one is that there is a problem with the quality or life of the oil-water separator itself; the other is that the quality of the air compressor oil is not up to standard, and its ability to separate from air is poor. At this time, the oil separator or air compressor oil should be replaced.
- Temperature sensor and computer failure, abnormal reading.
The influence of air compressor oil
- The oil quantity of the air compressor is insufficient.
During the operation of the air compressor, if the oil level of the air compressor is lower than the low oil level mark L or MIX, the air compressor oil is insufficient. Insufficient oil in the air compressor makes the heat dissipation worse, causing high temperature in the compressor. At this time, you should stop and refuel immediately.
- Air compressor oil deteriorates.
Oxidation and deterioration of compressor oil due to its own quality problems or exceeding the use time will lead to poor fluidity of the oil and a decrease in heat exchange capacity, resulting in the inability to completely and timely remove the heat from the head of the air compressor. Stop immediately for an oil change.
- Improper choice of air compressor oil viscosity.
If the viscosity of the air compressor oil is too low, the lubrication will be poor, which will cause abnormal wear of the equipment and excessive heat generation; Therefore, when maintaining the compressor, the user should refer to the service manual of the compressor and the actual working conditions of the user to select the appropriate viscosity grade.
- The quality of air compressor oil is not up to standard.
The main points are as follows: a. The thermal oxidation performance of air compressor oil is poor, and deposits such as sludge and paint film are generated during use, which affects the fluidity of the oil and reduces the lubricating performance of the oil; b. The viscosity-temperature performance of the oil is poor, the low-temperature fluidity is not enough, and the high-temperature lubricity is poor; c. The air separation ability of the air compressor oil is poor, which affects the separation of oil and gas.
The above is the cause analysis of common high temperature faults of screw air compressors. So for users, how to avoid or find compressor failures in time, so as to reduce production accidents and cost losses?
Environmental and Equipment Factors
- Arrangement of air compressor station.
When installing an air compressor station, it is necessary to pre-design the location of common equipment such as air compressors, air storage tanks, desiccants, filters, etc., and reserve enough space for heat dissipation and maintenance between equipment and equipment and between equipment and walls. space. The air compressor station should be well ventilated and an exhaust fan should be installed if necessary. If the air compressor station is built outdoors, it needs to be dustproof, waterproof, antifreeze, and explosion-proof to avoid abnormal damage to the air compressor caused by dust, moisture, extreme high and low temperature, etc. In addition, it is best to reserve an area for air compressor inspection and maintenance in the air compressor station, which is based on the largest area required for air compressor inspection and maintenance in the air compressor station, so as to ensure timely and convenient maintenance when the air compressor fails.
- Regular maintenance. Develop a good habit of regular inspection and maintenance, and form maintenance and repair records.
The scope of inspection includes compressed air and air compressor oil leakage, regular replacement of lubricating grease and other vulnerable parts as required, regular inspection of the voltage and current of the air compressor station, and cleaning and maintenance of the surface of the air compressor and other equipment. Environmental cleanup, etc. For detailed inspection and maintenance, please refer to the equipment maintenance manual.
Select qualified accessories
This includes common wearing parts such as air filters, oil-water separators, and air compressor oil for lubrication. Regarding the selection of air compressor oil, the following suggestions are given:
- Choose the right viscosity and choose the compressor oil with good viscosity-temperature performance.
The choice of compressor oil viscosity is based on the ability to balance lubricity and fluidity. If the working condition of the air compressor is not special, the user can choose according to the equipment manual; if the working condition of the air compressor is special, it needs to be adjusted appropriately according to the actual working condition. For example, if the working temperature of the air compressor station is high, the influence of temperature on the viscosity needs to be considered, and the viscosity can be increased appropriately; if the air compressor station is outdoors, and the temperature difference between day and night is relatively large, it is necessary to choose an air compressor oil with better viscosity-temperature performance, etc. .
- Choose compressor oil with good thermal oxidation stability.
For air compressors, due to the compressed gas, the 20% oxygen content is really a big test for the anti-oxidation performance of the compressor oil. Good thermal oxidation stability can not only prolong the service life of compressor oil, but more importantly, it can reduce the deposition and accumulation of sludge, paint film and other substances caused by high temperature oxidation, which cause high temperature of the compressor and affect the normal operation of the compressor very important factor. In addition, the acidic substances produced by oxidation also have adverse effects on the metal parts in the compressor to a certain extent.
- Choose compressor oil with good air separation performance.
The control of air release and foam will firstly affect the lubricity of the compressor, secondly, it will affect the effect of oil-gas separation of the compressor, and to a certain extent, it will also affect the service life of the oil-gas separator. In addition, if the oil-gas separation effect is not good, the oil content in the compressed air will be too high, which will affect the subsequent production and product quality.
- Consider the water resistance of the compressor oil.
Especially for coastal areas, outdoor air compressor stations, etc. where the air humidity is high, the moisture content in the air is high, and the existence of condensed water will easily cause emulsification of the compressor oil, thereby affecting the performance of the compressor oil. Therefore, it is necessary to choose a water-resistant Good compressor oil.
- Do a good job in oil product testing and tracking.
If conditions permit, regular oil testing is necessary for users. Through regular sampling to detect the performance changes of the compressor oil, the potential problems and failures of the compressor can be discovered in time through the performance changes, and at the same time, more accurate oil change instructions can be given to the user to avoid oil waste.
Sollant Focus on Energy Saving