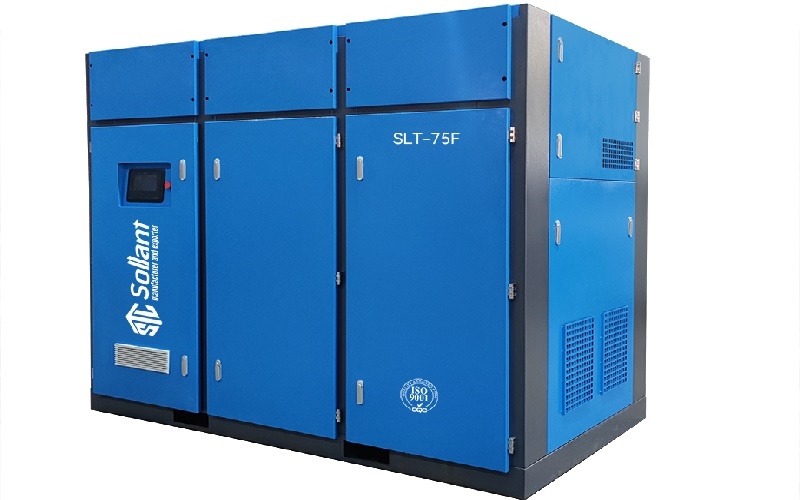
A rough analysis of the problem of oil leakage in automobile air compressors
For cars using air brakes, in order to ensure reliable and effective braking, the oil content in the compressed air must be strictly controlled. Too much oil in the compressed air will pollute the brake system, cause brake failure and cause traffic accidents, resulting in serious loss of life and property.
The oil in the compressed air is mainly due to the upward movement of the lubricating oil in the crankcase of the air compressor. Therefore, the oil supply function of the piston ring and the process of improving the upward movement of the lubricating oil must be solved.
In order to resist the upward movement of lubricating oil through the gap of the ring groove, twisted rings have been widely used in vehicle air compressors, and their structural forms are more common.
- Positive twisted rings are grooved or chamfered on the inner or outer edge of the rectangular cross-section ring. When installing, the grooves or chamfers on the inner edge are upward and the grooves or chamfers on the outer edge are downward. When the twisted ring moves up and down, it will produce obvious dish-shaped deformation, so that the edge of the ring is in linear contact with the side wall of the ring groove and the cylinder wall.
- This not only reduces the oil pumping effect of the piston ring, but also improves the airtight performance of the piston ring. The wedge-shaped ring formed by the grooved or chamfered positive twist ring on the outer edge and the cylinder wall can distribute oil upward and scrape oil downward, which not only covers the lubrication between the cylinder wall and the piston (piston ring) group, but also Reduced the up channeling of lubricating oil. The first sealing ring is prone to early wear due to the greater gas pressure, so it is advisable to use a positively twisted ring with grooves or chamfers on the inner edge.
- Anti-twist rings are similar in construction to normal twist rings, except that they are installed in the ring in reverse, with the inner edge notched or chamfered downwards and the outer edge notched or chamfered upwards. Therefore, under the action of gas pressure, the twisted ring can produce a dish-shaped deformation opposite to that of the normal twisted ring, which can better inhibit the upward movement of lubricating oil. However, due to the inverted wedge shape formed by the outer edge of the ring and the cylinder wall, it is scraped into the cylinder to cause oil blow-by. Therefore, it is not suitable for use as the first sealing ring.
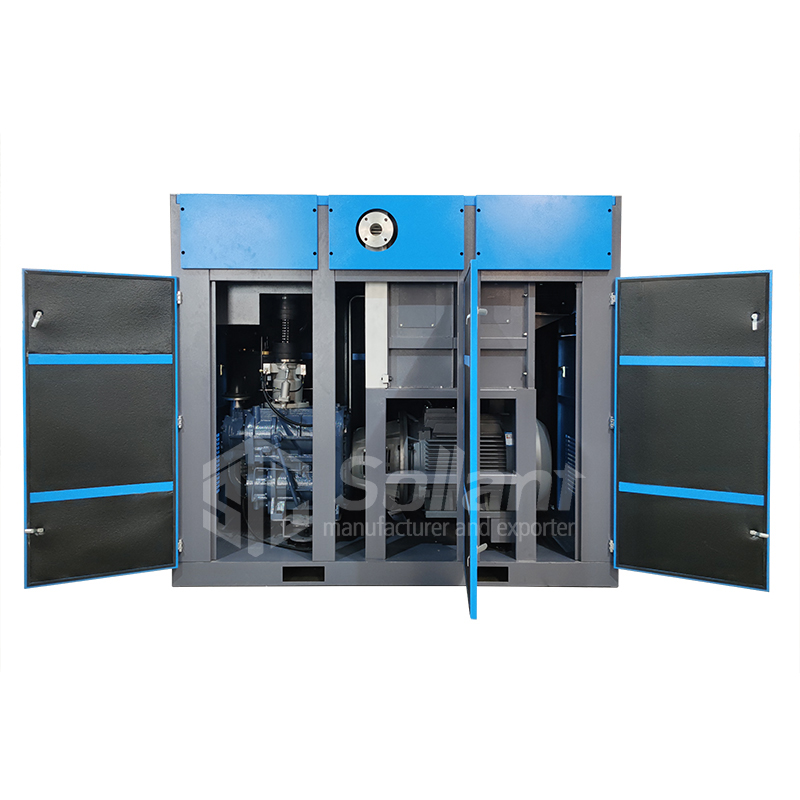
Improvement of Piston Ring Groove
The improvement of the piston ring groove is mainly to control the assembly gap between the piston ring and the ring groove, and to improve the surface roughness and shape tolerance of the ring groove.
For example, the assembly side clearance of the piston ring and the ring groove of Dongfeng Air Compressor is changed from 0.04mm~0.08mm to 0.04mm~0.065mm, and the verticality error of the side wall of the control ring groove to the center line of the piston is not more than 0.01mm per 100mm sampling length , Surface roughness Ra=1.6, in order to ensure a good fit between the ring and the ring groove, improve the air tightness of the cylinder and reduce the lubricating oil.
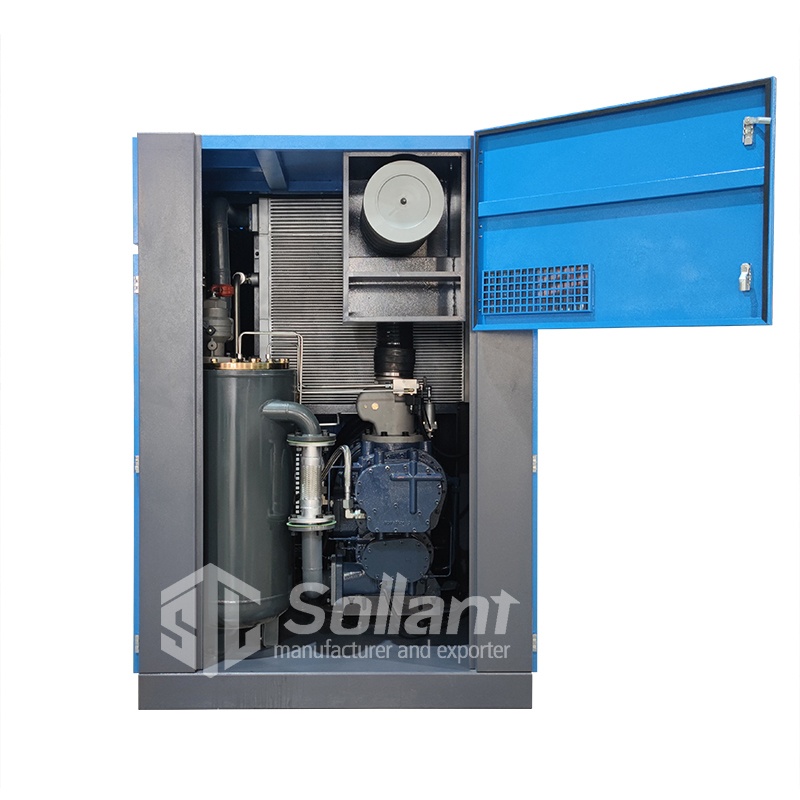
Influence of Piston Ring's Directional Cut-off Load and Lateral Force
The direction interception load of the piston ring to the cylinder wall includes the initial elastic force of the piston ring and the gas pressure during the operation of the air compressor, which is the main reason for the wear of the piston ring and the cylinder wall, especially the wear of the first air ring is greater. Oil blow-by of piston rings and cylinder walls will increase as wear increases.
In order to reduce the amount of upward channeling of lubricating oil, the wear of piston rings must be controlled. For this reason, the material of the piston ring should be a material with high wear resistance, hardness and toughness, and the matching clearance between the piston and the cylinder wall should be strictly controlled.
Influence of Oil Return Section at the Bottom of Oil Ring Groove
The lubrication of the cylinder wall of the vehicle air compressor usually relies on splash lubrication, but when the lubricating oil pressure in the crankcase is high, the amount of splash increases, and if the oil ring scrapes oil poorly, it will lead to oil leakage. Therefore, increasing the cross section of the oil return hole can resist oil leakage.
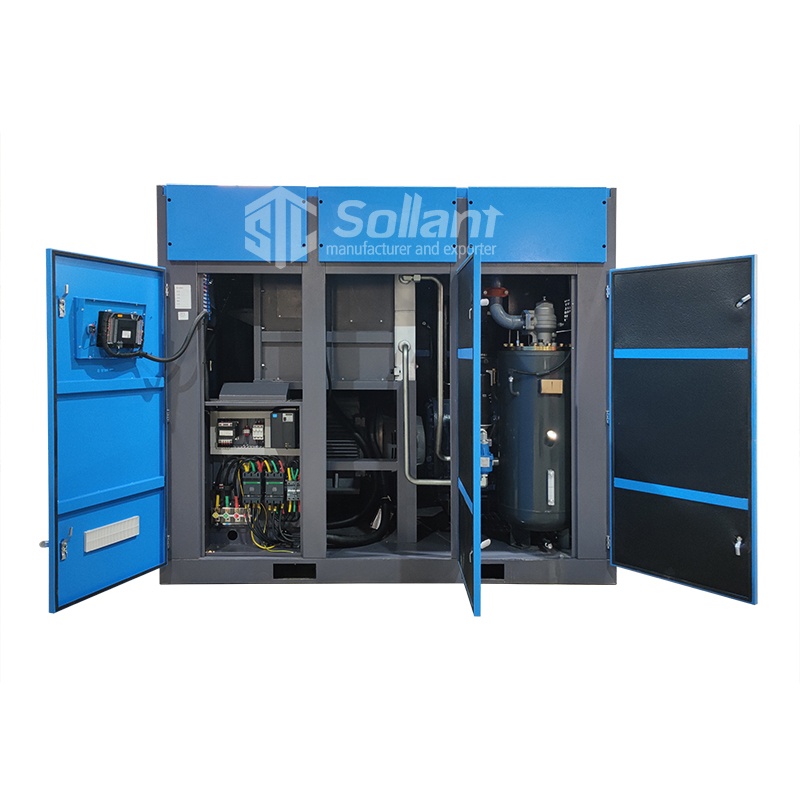
Effect of temperature
When the air compressor is working, due to the compression of the gas and the friction of the moving parts, the temperature of the body will increase and the viscosity of the lubricating oil will be reduced, thereby aggravating the upward movement of the lubricating oil. For this reason, the specifications and models of engine oil should be selected reasonably according to the region and season.
Effects of clogging and overpressure
The oil return pipe of the air compressor is blocked. Because the engine air pump is supplied with oil from the main oil passage of the engine, if the oil return pipe of the air compressor is blocked, the oil cannot return to the oil pan of the engine, causing the crankcase of the air compressor to be filled with oil, the oil level rises, and the oil It is forced to escape into the cylinder and cause oil to escape.
At the same time, it will also cause serious oil leakage at both ends of the air pump. The air filter core on the air compressor is clogged, which increases the air intake resistance of the air pump, reduces the intake air volume, and the air in the cylinder becomes thinner, thereby increasing the oil absorption effect of the cylinder and causing the air compressor to blow oil. The oil pressure of the engine is too high, and sometimes the air compressor will leak oil.
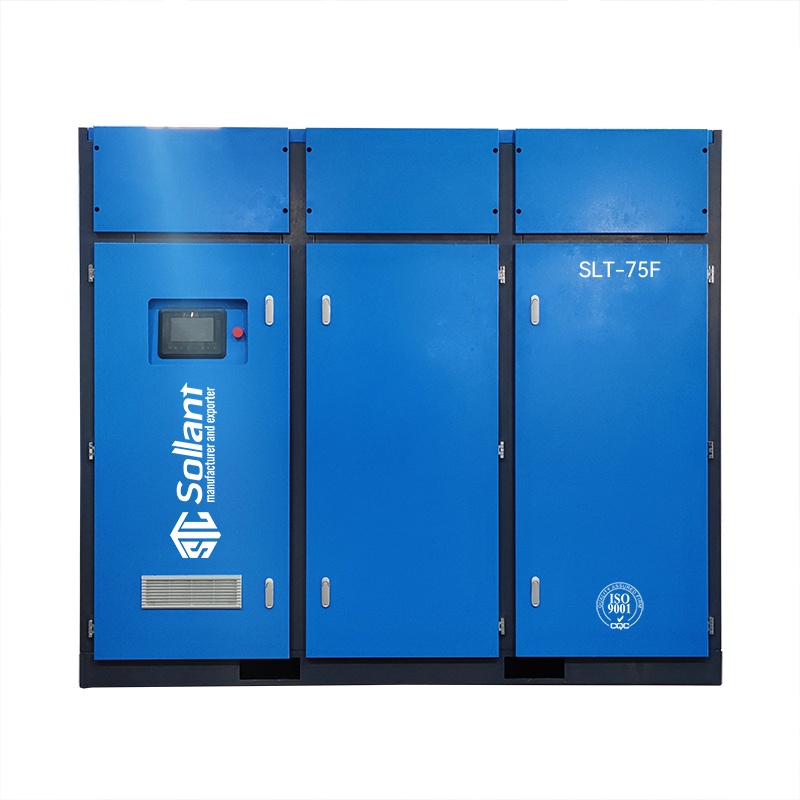
The hazards of oil leakage in air compressors
For cars using air brakes, in order to ensure reliable and effective braking, the oil content in the compressed air must be strictly controlled. Too much oil in the compressed air will pollute the brake system, cause brake failure and cause traffic accidents, resulting in serious loss of life and property.
The oil in the compressed air is mainly due to the upward movement of the lubricating oil in the crankcase of the air compressor. Therefore, the oil supply function of the piston ring and the process of improving the upward movement of the lubricating oil must be solved.
- After the oil from the air compressor escapes, the oil will enter the air storage tank of the car. When the car brakes, the oil will enter the brake valve. After a long time, the rubber seal in the valve will expand and loosen, causing judgment The motion control does not work. At the same time, engine oil will also cause early corrosion damage to brake hoses and brake cups, which will affect driving safety.
- After the engine oil enters the cylinder head of the air compressor, due to its high height, the exhaust valve and valve spring on the cylinder head of the air compressor are prone to cementation, which affects the normal operation of the air compressor, and finally causes the air compressor to The machine does not work.
- After the air compressor leaks oil, it will increase the oil consumption of the engine, which will affect the lubrication of the engine, increase the transportation cost of the vehicle, and make the engine discharge exceed the standard, causing environmental pollution.
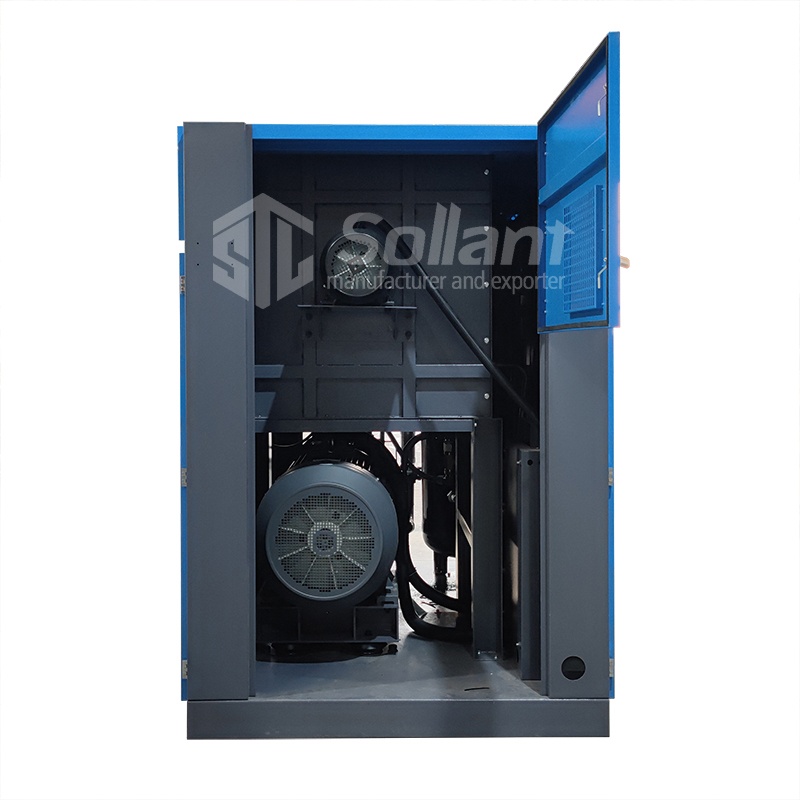
Through the improvement of the ring groove of the piston ring, the surface roughness and assembly precision are improved, and the airtightness of the ring and the ring groove in the cylinder is guaranteed. Use improved piston ring grooves, reasonably select and correctly assemble piston rings, and consider factors such as materials and operating temperature; often check whether the oil return line and air intake are unblocked, and replace engine oil and oil filter elements according to standards, which can effectively control the air pressure. The hazards of machine oil leakage are better controlled and resolved.