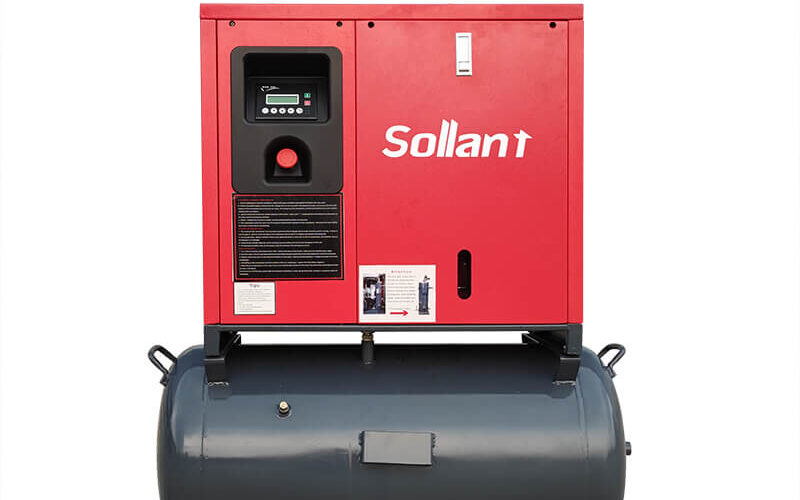
Common maintenance methods for piston air compressors
The common maintenance methods of piston air compressors are mainly divided into four major methods: overhaul, medium repair, minor repair and daily maintenance. The following describes the specific content of each.
- Overhaul
Overhaul is to disassemble all compressor parts, replace all worn parts, check all parts of the compressor, and eliminate all faults of the compressor. Overhaul cycle: general air compressors run for 20,000h to 26,000h for one overhaul, and each overhaul takes 7 to 15 days; large-scale process compressors run for 14,000h for one overhaul, each time about 15 days. The main contents of the overhaul are:
(1) Check whether there are cracks in the crankshaft, the conicity and ellipticity of the main journal of the crankshaft, and the connection between the balance iron and the crankshaft.
(2) Check or replace the crosshead pin and piston pin.
(3) Check all bearings for wear, and replace severely worn bearing bushes.
(4) Check whether the relative position of the connecting rod, piston and crankshaft is skewed.
(5) Check whether the connecting rod bolts have tensile deformation, cracks, wear, etc.
(6) Check the fixation of the piston and the piston rod, and check whether there is any jumping deviation of the piston rod during the movement.
(7) Clean the cylinder and piston, check their wear and repair.
(8) Replace all vulnerable parts of the compressor, such as piston rings, valve plates, etc.
(9) Check all safety valves and adjust their opening pressure to meet the specified requirements.
(10) Check all instruments, meters, verification date, sensitivity and working condition.
(11) Detect and adjust the levelness of the crankshaft, the levelness of the cylinder, the clearance between the cylinder and the piston, the perpendicularity between the crankshaft and the piston rod and the cylinder, the connection between the crosshead and the piston rod, the radial clearance between the big end of the connecting rod and the crankshaft and the axis to the gap.
(12) Check the connection between the compressor and the motor.
(13) After the overhaul, the compressor unit, auxiliary equipment, pipelines, etc. should be painted or repainted.
(14) After the overhaul, various performance tests, pressure tests, and test runs should be carried out on the compressor, and corresponding overhaul records should be made.
- Medium repair
The air compressor shall be repaired every 3000h~6000h, and the gas compressor shall be repaired every 2330h~5500h. The scope of each repair is about 4-5 days. Also smaller. The main content of medium repair is to repair vulnerable parts, check the tightness of pressure gauges, safety valves and other valves.
During the medium repair process, if the following parts are found to be worn, they should be replaced: sealing elements of packing, sealing elements in oil scraper, air valve, small piston of unloading valve, piston ring, connecting rod bearing bush, crosshead bushing and non-lubricated of various parts.
- Minor repairs
Minor repairs of piston compressors are irregular, about once every 4 to 8 days, and the contents of the repairs can also be determined according to the actual situation. One or more of the following can be selected:
(1) Clean the gas storage tank, filter, exhaust pipe, valve, cooling water jacket of the compressor, cooling water pipe of the intercooler, oil filter, oil pipe, pressure regulator and unloading valve device, etc.
(2) Check the fit clearance of the crankshaft, connecting rod, crosshead and other parts of the compressor movement mechanism.
(3) Check the fastening condition of bolts and gaskets at each connecting part, and replace them if necessary.
(4) Check whether the action of the test safety valve, pressure regulator and unloading valve is sensitive.
(5) Check the wear of the cylinder piston ring, and replace it if the wear is serious. Check all parts of the air valve, such as valve plate, valve seat, spring, etc., and replace them if they are damaged, deformed, twisted, etc.
- Daily maintenance
In order to ensure the normal operation of the compressor, some small faults that occur during the operation of the compressor must be eliminated and repaired in time. Such as water leakage and oil leakage in the cooling water system and lubricating oil system, loosening of bolts, failure of air valves, etc., as well as abnormal vibration, noise, overheating, etc.
In short, practice has proved that as long as the operating procedures are strictly followed. Strengthening the awareness of daily maintenance of the compressor, and timely maintenance management can ensure that the compressor operates under the best working condition. Extend the service life of the compressor and achieve a satisfactory use effect.
Sollant Focus on Energy Saving