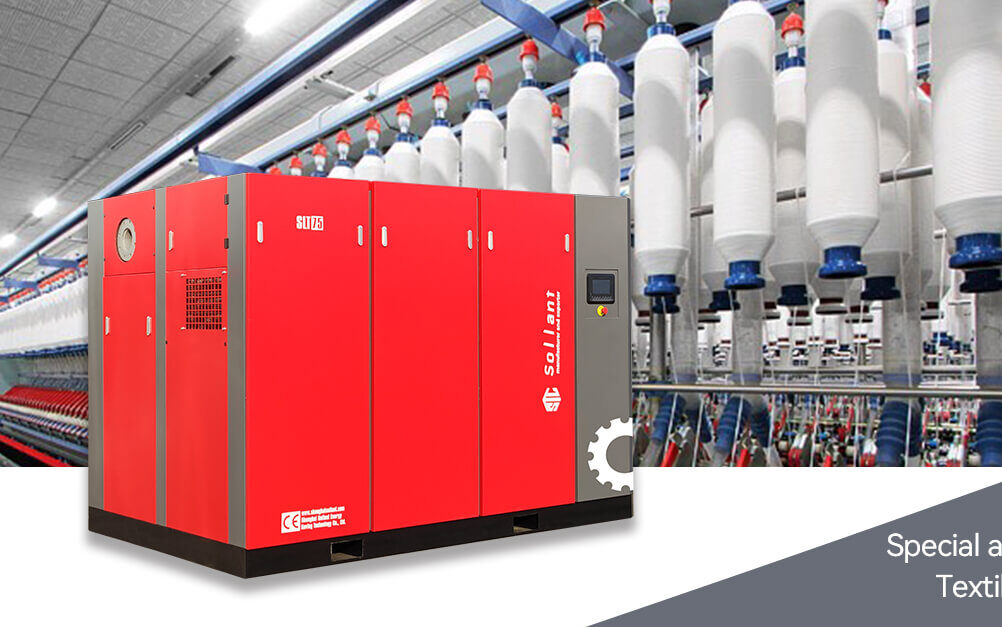
Common reasons for the serious heating of the screw air compressor motor
- The air gap between the stator and rotor of the motor is very small, which may easily lead to collision between the stator and rotor
In medium and small motors, the air gap is generally 0.2mm to 1.5mm. When the air gap is large, the excitation current is required to be large, thereby affecting the power factor of the motor; if the air gap is too small, the rotor may rub or collide. Generally, due to the serious out-of-tolerance of the bearing and the wear and deformation of the inner hole of the end cover, the different axes of the machine base, end cover and rotor will cause bore sweeping, which will easily cause the motor to heat up or even burn out. If the bearing is found to be worn, it should be replaced in time, and the end cover should be replaced or brushed. The simpler treatment method is to inlay the end cover.
- The abnormal vibration or noise of the motor can easily cause the motor to overheat
This situation belongs to the vibration caused by the motor itself, most of which are due to poor dynamic balance of the rotor, poor bearing, bent shaft, different shaft centers of the end cover, machine base, and rotor, loose fasteners, or uneven foundation of the motor installation, and improper installation It may be caused by the transmission from the mechanical end, which should be ruled out according to the specific situation.
- If the bearing is not working properly, it will definitely cause the motor to overheat. Whether the bearing is working normally can be judged by hearing and temperature experience.
You can check the bearing end with your hands or a thermometer to determine whether its temperature is within the normal range; you can also use a listening rod (copper rod) to touch the bearing box. If you hear an impact sound, it means that one or several balls may be crushed. Hissing sound, it means that the lubricating oil of the bearing is insufficient, and the motor should change the lubricating grease every 3000 hours to 5000 hours.
- The power supply voltage is too high, the excitation current increases, and the motor will overheat
Excessive voltage can compromise the motor insulation, putting it at risk of breakdown. When the power supply voltage is too low, the electromagnetic torque will decrease. If the load torque does not decrease and the rotor speed is too low, the increased slip will cause the motor to be overloaded and heat up. Long-term overload will affect the life of the motor. When the three-phase voltage is asymmetrical, that is, when the voltage of one phase is high or low, the current of a certain phase will be too large, and the motor will heat up. At the same time, the torque will decrease and the “humming” sound will be emitted. After a long time, the winding will be damaged.
In short, no matter whether the voltage is too high, too low or the voltage is asymmetrical, the current will increase, and the motor will heat up and damage the motor. Therefore, according to the national standard, the change of the power supply voltage of the motor should not exceed ±5% of the rated value, and the output power of the motor can maintain the rated value. The motor power supply voltage is not allowed to exceed ±10% of the rated value, and the difference between the three-phase power supply voltages should not exceed ±5% of the rated value.
- Winding short circuit, turn-to-turn short circuit, phase-to-phase short circuit and winding open circuit
After the insulation between two adjacent wires in the winding is damaged, the two conductors touch each other, which is called winding short circuit. Winding short circuits that occur in the same winding are called turn-to-turn short circuits. A winding short circuit that occurs between two phase windings is called a phase-to-phase short circuit. No matter which one it is, it will increase the current of one phase or two phases, cause local heating, and age the insulation to damage the motor. Winding open circuit refers to the failure caused by the stator or rotor winding of the motor being broken or blown. Whether it is a short circuit or an open circuit of the winding, it may cause the motor to heat up or even burn out. Therefore, it must be shut down immediately after this happens.
- The material leaks into the motor, which reduces the insulation of the motor, thereby reducing the allowable temperature rise of the motor
If solid material or dust enters the motor from the junction box, it will reach the air gap between the stator and rotor of the motor, causing the motor to sweep, until the insulation of the motor winding is worn out, and the motor is damaged or scrapped. If liquid and gaseous media leak into the motor, it will directly cause the insulation of the motor to drop and trip. General liquid and gas leakage has the following manifestations:
(1) Leakage of various containers and delivery pipelines, leakage of pump body seals, flushing equipment and ground, etc.
(2) After the mechanical oil leaks, it enters the motor from the gap of the front bearing box.
(3) The oil seal of the reducer connected to the motor is worn, and the mechanical lubricating oil enters along the motor shaft. After accumulating inside the motor, it dissolves the motor insulation varnish and gradually reduces the insulation performance of the motor.
- Almost half of the motor burns are caused by the lack of phase operation of the motor
The lack of phase often causes the motor to fail to run or the speed is slow after starting, or there is a “humming” sound when the rotation is weak and the current increases. If the load on the shaft does not change, the motor is seriously overloaded, and the stator current will reach 2 times the rated value or even higher. The motor will heat up or even burn out in a short time. The main reasons for the lack of phase operation are as follows:
(1) If one phase of the power line is cut off due to failure of other equipment, other three-phase equipment connected to the line will run without phase.
(2) One phase of the circuit breaker or contactor is out of phase due to bias voltage burnout or poor contact.
(3) The lack of phase caused by the aging and wear of the incoming line of the motor.
(4) One-phase winding of the motor is broken, or one-phase connector in the junction box is loose.
- Other non-mechanical and electrical failure causes
The temperature rise of the motor caused by other non-mechanical and electrical faults may also lead to motor failure in severe cases. If the ambient temperature is high, the motor lacks a fan, the fan is incomplete, or the fan cover is missing. In this case, it is necessary to force cooling to ensure ventilation or replace fan blades, otherwise the normal operation of the motor cannot be guaranteed.
To sum up, in order to use the correct method to deal with motor faults, it is necessary to be familiar with the characteristics and causes of common motor faults, grasp the key factors, and conduct regular inspection and maintenance. In this way, detours can be avoided, time can be saved, faults can be eliminated as soon as possible, and the motor can be in a normal operating state, thereby ensuring the normal production of the workshop.
Sollant Group-Professional Compressed Gas Solutions Provider