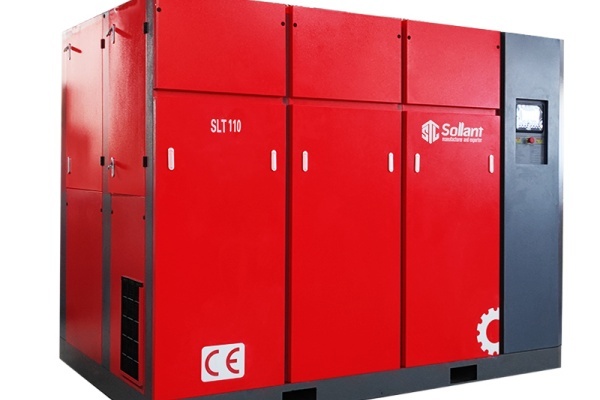
Screw compressor machine Daily operation and maintenance
The daily operation and maintenance of screw compressor machine are crucial aspects to ensure their smooth functioning and extend their service life. Below is a detailed elaboration on these two aspects:
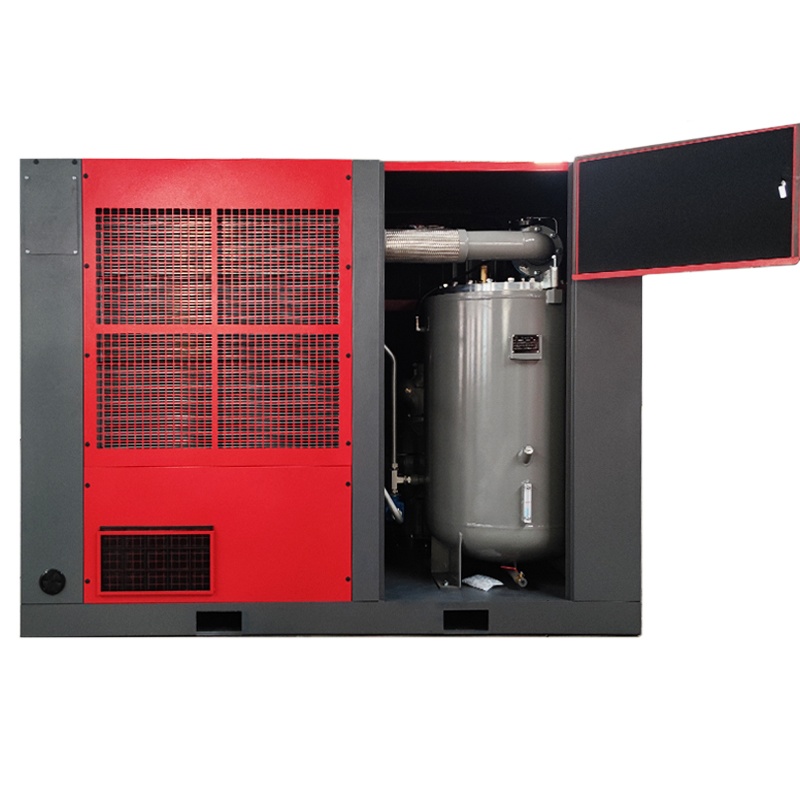
Daily Operation
- Pre-startup Preparation
- Check Oil Level: Ensure that the oil level in the oil-gas separator is above the minimum mark. If the oil level is low, add lubricant oil after shutting down the compressor, releasing pressure, and loosening the oil filler plug.
- Drain Condensate Water: Slightly open the drain valve at the bottom of the oil-gas separator to drain any condensate water. Tighten the valve once the water is drained.
- Inspect Connections: Check for any air, oil, or water leaks at all connection points.
- Check Power Supply: Confirm that power has been supplied and the indicator lights are on.
- Startup Procedure
- Start the screw compressor machine: Press the “Start” button. The “Start” indicator light should illuminate, and the compressor should begin running.
- Observe Operating Status: Check if the screw compressor machine automatically loads, the inlet valve opens, and the lubricant oil pressure gauge and discharge pressure gauge needles rise. Also, verify that the oil level is within the normal range and there are no leaks at the connection points.
- Operation Monitoring
- Periodically Check Parameters: Record operating parameters such as voltage, current, discharge pressure, discharge temperature, and oil level for future reference.
- Attention to Abnormalities: Stop the compressor immediately if abnormal vibrations, noises, or oil leaks occur.
- Shutdown Procedure
- Normal Shutdown: Press the “Unload” button and let the screw compressor machine run for at least 20-30 seconds to unload. Then, press the “Stop” button for a soft shutdown.
- Emergency Shutdown: In case of emergencies (e.g., motor or electrical fire, mechanical knocking sounds, or significant noise increase), immediately press the emergency stop button.
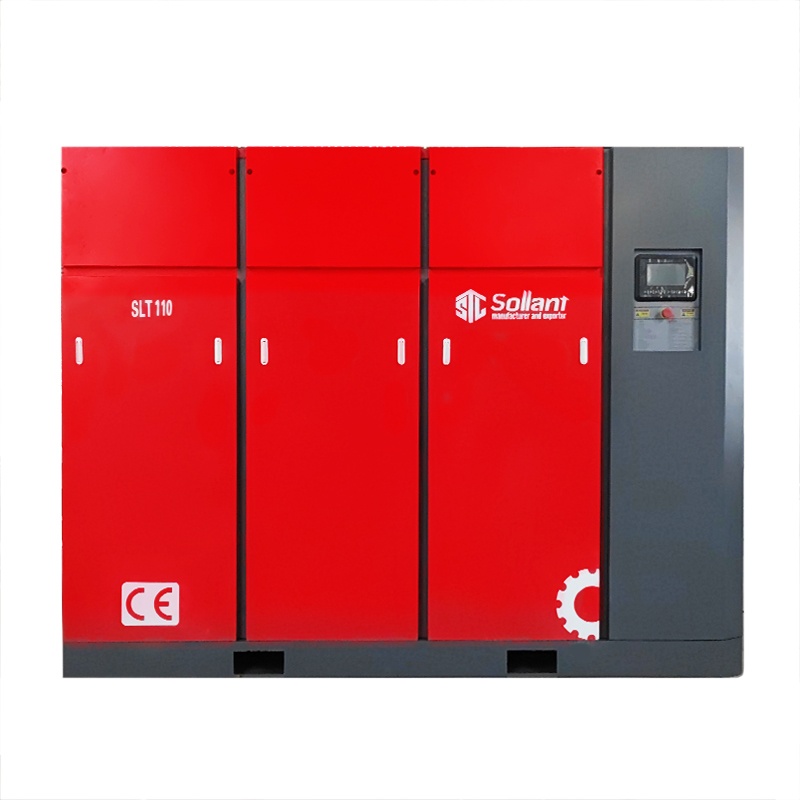
Maintenance
- Regularly Check and Replace Filters
- Use filters to remove impurities and moisture from the air to ensure air quality and compressor operation. Regularly inspect and clean filters, replacing them as needed based on usage.
- Regularly Clean the Cooler
- The compressor cooler, located externally, is prone to dust and oil contamination. Regular cleaning maintains its surface cleanliness, ensuring cooling efficiency and heat dissipation.
- Regularly Check Lubricating Oil
- Lubricating oil is crucial for the smooth operation of internal compressor components. Regularly inspect oil quality and quantity, replacing or topping up as necessary. Also, check for cracks or damage to the oil level gauge and replace if found.
- Clean and Maintain the Compressor Interior
- Regular cleaning and maintenance of the compressor interior are key maintenance steps. After shutting down the power and discharging compressed air, open the compressor’s covers and panels, using cleaning agents and tools to clean internal components and ensure parts are intact.
- Regularly Check and Calibrate the Control System
- The compressor’s control system monitors and controls its operating status. Regular checks and calibrations ensure accuracy and reliability.
- Other Maintenance Items
- Regularly inspect and clean the fan to ensure proper operation and cooling.
- Check and replace belts periodically to maintain transmission efficiency.
- Perform regular maintenance on the compressor’s oil-gas separator to maintain its separation efficiency.
- Regularly inspect the electrical system to ensure secure wire connections and proper functioning of control system terminals.
- Conduct periodic full-system operational tests to ensure the compressor’s performance and operating status meet requirements.
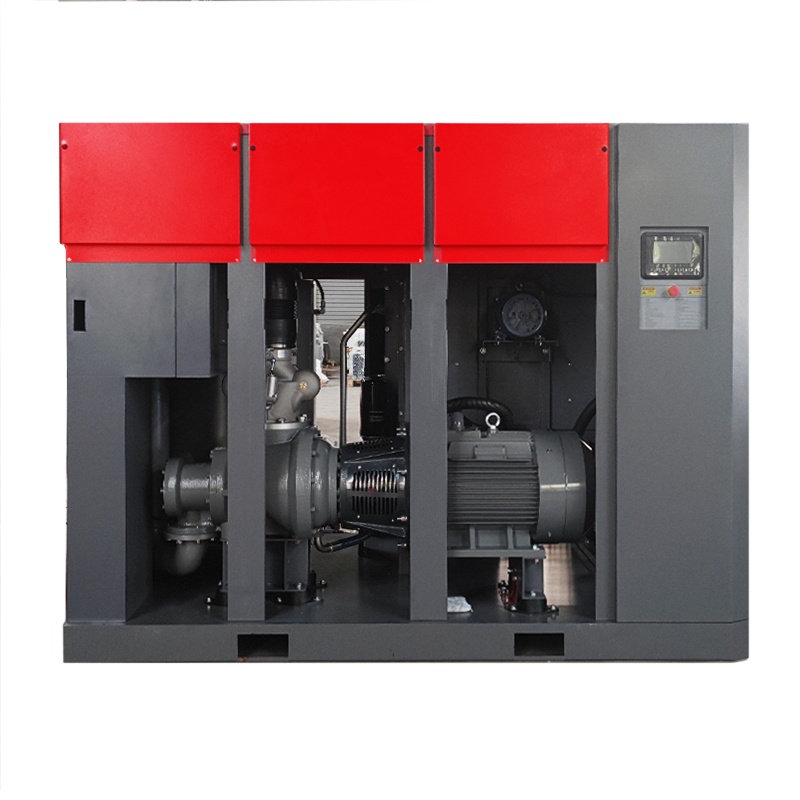
By standardizing daily operation and maintenance procedures, the stable operation and extended service life of screw air compressors can be ensured. Additionally, adhere to safety regulations during operation to prevent accidents.